Understanding the Origin of Metal in Dairy Processing
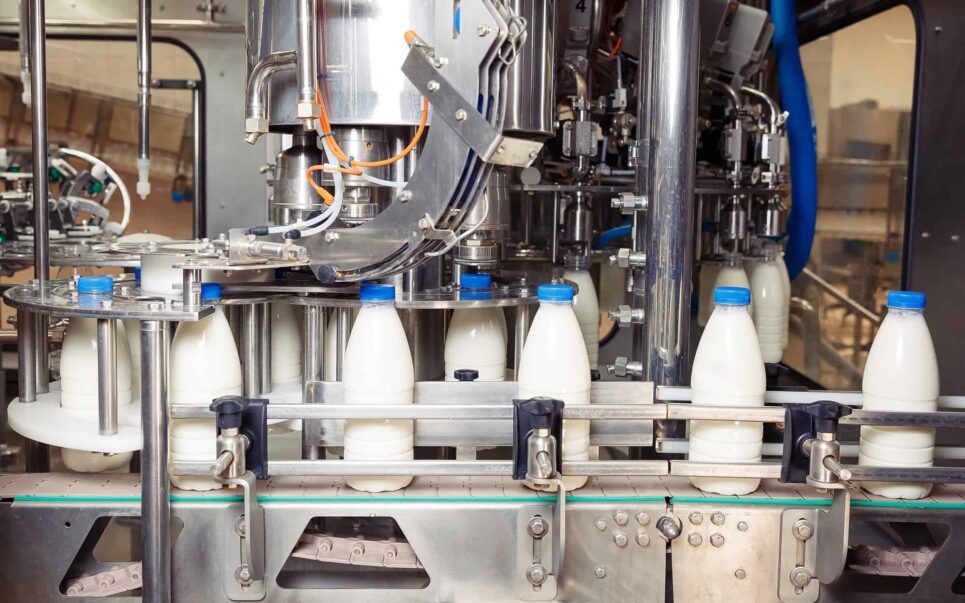
In the dairy processing industry, nothing is more important than the safety and quality of the finished products. However, one of the unsuspecting issues that compromise this essential aspect is metal contamination. But where does this metal originate from, and why is it found in dairy processing?
Read on to learn more about metal in dairy processing.
Dairy Processing Explained
Dairy processing constitutes a precise multi-stage system that hinges on strict protocols to safeguard product quality and safety. From the initial step, which is the collection of raw materials, to the delivery of the final product, exceptional care and diligence are mandatory to avoid and reduce risk of any form of contamination, including the presence of metals. Understanding these processes is fundamental in grasping where metal comes from in dairy processing. An exhaustive explanation of the dairy processing journey aids in identifying the genesis of potential contaminants.
Collection and Transportation of Raw Dairy Products
In the initial dairy processing phase, raw dairy products are collected from dairy farms and transported to the processing plants. Milk, for instance, is harvested directly from dairy cows meticulously. The milking equipment is often constructed from materials like stainless steel, which if corroded or improperly handled, can contribute to metallic contamination. Furthermore, transportation vehicles and storage containers made from metals can also be a source of contamination if not maintained properly.
According to the World Health Organization, the quality of raw materials significantly determines the overall quality and safety of the final dairy product. To forestall heavy metal in dairy products, a critical assessment of the collection and transportation of raw products is indispensable. This includes rigorous inspection of the milking devices, transportation vehicles, and storage containers to ensure they meet the agreed safety standards.
Pasteurization and Homogenization
Pasteurization is a vital process in dairy manufacturing that involves heating of the products to kill harmful microorganisms, thereby enhancing the product’s safety for consumption and extending its shelf life. Homogenization, on the other hand, is the process of breaking down the fat molecules in milk to create a smooth, uniform texture. Although these major phases transform raw milk into consumable dairy products, they are also potential arenas for the introduction of metal contaminants.
Key among the potential culprits are the processing machines. These are primarily made of metals such as stainless steel, and exposure to high temperatures and pressures, normal wear and tear, or machine faults can cause metallic fragments to mix with the dairy products. The European Food Safety Authority emphasizes the role of regular and meticulous maintenance and inspection of processing machinery, quick replacement of worn-out parts, and employing efficient detection systems as a corrective measure to counteract this problem.
Packaging and Delivery
Dairy products are then packaged into containers, such as milk bottles or yogurt cups, and prepared for shipment to retail stores or direct consumer delivery.
Explore different types of magnetic separators that help prevent metal contamination in dairy processing.
The Role of Equipment: Sources of Metal in Dairy Processing
The dairy processing industry primarily utilizes machinery and utensils made from stainless steel, recognizing its durability and resistance to corrosion. However, while these beneficial characteristics make stainless steel ideal for manufacturing processes, it also poses a potential source of metal in dairy processing. With prolonged use, metal swarf or tiny metallic fragments can break off from the working surfaces of equipment or utensils and contaminate the products being processed.
Equipment Wear & Abrasion
Stainless steel is the preferred choice when it comes to manufacturing equipment and utensils in the dairy processing industry. Renowned for its strength and high resistance to staining and rusting, stainless steel is considered a hygienic material appropriate for food preparation and handling. However, among all the benefits stainless steel brings to the dairy processing industry, one significant concern persists: it can be a source of metal contamination.
As stainless steel machinery and pipework wears down over time, usually from abrasion from various products such as lactose, metal particles can shed off during processing and find their way into the dairy products.
Abrasive products are not the only cause for machine wear in dairy processing. Another example of equipment wear happens during pumping of the milk – incidental pump wear or breakage of fragments from pump breakdowns occurs and poses a contamination risk.
Spray Dryer
Another source of metal contamination in dairy processing is the spray dryer. The gas burners on the spray dryer run so hot that the particles burn and create a burnt scale on the surface of the dryer. This scale is basically ash, and this particular ash is magnetic and can be removed by high intensity magnets.
Dairy Processing Machinery: High-Risk Factors
Certain machines used in dairy processing are highly susceptible to wear and tear due to their heavy usage and complexity. These high-risk machines include milk pasteurizers, homogenizers, separators, and packaging equipment. Their intricate mechanisms and numerous moving parts present numerous chances for metal fragments to break off and into the product during operation.
Preventative Measures Against Metal in Dairy Processing
Metal contamination can impact the safety of your dairy products and in turn, your consumers, leading to product recalls and customer complaints. That’s why the dairy industry relies on specialized magnetic separators to ensure high-quality and contaminant-free products.
Magnetic Separators
Let’s explore some quality magnetic separators from Magnattack® that help prevent metal in dairy processing:
- Mag-Ram® Self-Cleaning Magnet: A customizable, self-cleaning, sanitary design for dry powder applications.
- The Rapidclean® Drawer Magnet: A hygienic design. Easy cleaning and maintenance.
- Spherical Pneumatic Transfer Magnet and Powder Transfer Magnet: Sanitary magnets for high-velocity pneumatic transfer lines.
- Emulsion & Slurry Pipeline Separator: Designed for thick and viscous liquids and slurries.
Key Takeaways
Say goodbye to magnetic contamination in your processing lines with Magnattack® and Powder Process Solutions, our key partner in the dairy sector. Upgrade your processing facility with Magnattack® magnets and enjoy a peace of mind knowing that your products are designed for sensitive, hygienic dairy applications, free from and protect your final product from foreign metal fragment contamination. Contact us today to learn more about our line of magnetic separators for the dairy industry.