Reducing Metal Contamination in Food: A Milk and Dairy Guide
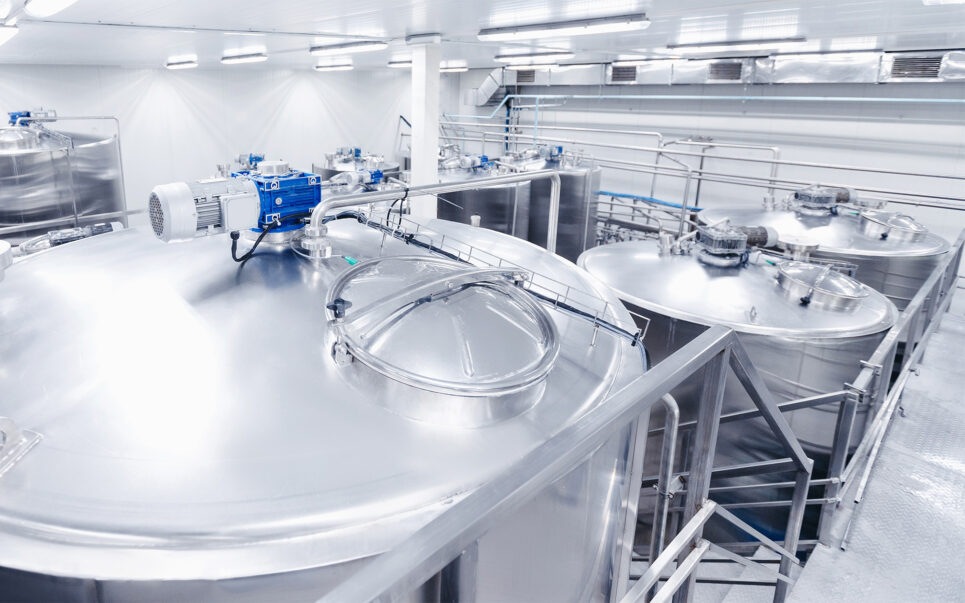
The concern about metal contamination in foods like the milk and dairy industry is undeniable. Milk and dairy products are vital components of a balanced diet, and contamination can pose serious health risks to consumers.
Understanding Metal Contamination in Dairy Products
Metal contamination in food, particularly dairy products, significantly challenges public health.
There are a few different causes of metal contamination in dairy products. Understanding the various metal contamination sources is crucial for implementing robust measures for contaminant removal.
How Milk Gets Contaminated by Metals
Various factors can cause metal contamination in milk and dairy. From collection of milk to the end of the processing of the product, there are many stages at which metal contamination is typically introduced.
An example of a source of metal contamination in dairy processing is equipment wear and abrasion. As stainless steel machinery and pipework wears down over time, usually from abrasion from various products such as lactose, metal particles can shed off during processing and find their way into the dairy products.
Abrasive products are not the only cause for machine wear in dairy processing. Another example of equipment wear happens during pumping of the milk – incidental pump wear or breakage of fragments from pump breakdowns occurs and poses a contamination risk.
Another source of metal contamination in dairy processing can be the spray dryer. The gas burners on the spray dryer run so hot that the particles burn and create a burnt scale on the surface of the dryer. This scale is basically ash, and this particular ash is magnetic and can be removed by high intensity magnets.
The Impact of Metal Contamination on Quality and Food Safety
Metal contamination in milk compromises the product’s safety and quality. Metals can cause oxidative damage, affecting dairy products’ flavor stability and shelf life. This directly impacts public health, as dietary exposure to heavy metals is linked with various adverse health effects.
Magnetic Separation in the Milk and Dairy Industry
Magnetic separation technology has been increasingly adopted in the milk and dairy industry to remove metal contamination. This method utilizes high strength sanitary magnetic separation devices to extract metallic particles from the product, aiding the removal of even the smallest metal fragments.
It is crucial that equipment installed in dairy processing plants is hygienic & dairy-grade in order to prevent serious contamination issues from occurring. If the equipment is not dairy-grade, there is a higher risk of product getting trapped in crevices, posing serious contamination and product security risks.
Wondering what options are out there for your dairy processing business? Find the right match for your needs and goals with insight into the different kinds of magnetic separators.
Magnetic Separators for Milk and Dairy Processing
Various magnetic separators are utilized in the milk and dairy industry, each designed to address specific challenges of metal contamination and different types of products processed.
Mag-Ram® Self-Cleaning Magnet
The Mag-Ram® Magnetic Separator boasts a patented design featuring tight wiper seals for effective cleaning and quick maintenance. Its standardized components and modular design reduce spare parts and downtime. With no sleeves to accumulate material or harbor bacteria, it meets hygienic standards. Offering in-stream or batch cleaning options, it allows for individual magnetic ram cleaning, preventing product exposure. Its enclosed mechanism ensures mechanical efficiency and sanitation, eliminating issues like “walking” and “jamming” seen in other designs.
RapidClean® Drawer Magnet
The Rapidclean® Drawer Magnet offers customizable magnet spacing for optimal foreign metal separation, crucial in sensitive applications handling tiny metal fragments. Its option for the Swing-Away Style door design facilitates easy access, ideal for tight installations with limited vertical space. Optional removable screen drawers filter out large contaminants, while exterior door guides prevent sticking and jamming, ensuring safe and efficient operation. USDA-certified models are available for sensitive product handling, with easy cleaning between batches.
Emulsion and Slurry Pipeline Separator
The Emulsion & Slurry Pipeline Separator utilizes Acutex® Probe Magnets to efficiently capture and retain foreign metal fragments in highly viscous product flows. Their lachrymiform or teardrop shape minimizes resistance and maximizes coverage without causing leaks or blockages. Positioned to face the product stream, the probes safely retain collected fragments until cleaning, reducing recontamination risks. Perpendicular placement creates a powerful magnetic matrix, ensuring comprehensive fragment capture in thick emulsions and slurries.
Spherical Pneumatic Transfer Magnet & Powder Transfer Magnet
The Spherical Pneumatic Transfer Magnets & Powder Transfer Magnets (link please) are dairy-grade magnetic separators which have had great success in pneumatic transfer lines in many industries, including dairy processing. The Spherical Pneumatic Transfer Magnet boast a high magnetic strength of up to approximately 12,000-13,000 gauss, double that of conventional alternatives such as bullet-style or catridge-style magnets. Positioned transversely to product flow, they efficiently retain metal fragments. Their compact design allows easy installation into existing or new processes with various connection fittings. The spherical shape of the Spherical Magnet and the Acutex® Probe design of the Powder Transfer Magnet minimizes re-contamination risks, making them more effective and user-friendly than traditional bullet-style magnets, with increased efficiency reported by various industries.
Discover the Solution to Metal Contamination in Food Processing With Magnattack
In the dairy industry, effective magnetic separation is crucial for ensuring product purity and safety by removing metal contaminants from food processing lines. Magnattack specializes in providing innovative magnetic separation solutions tailored to the unique needs of dairy processing facilities. Contact us today to experience our excellence in magnetic separators and beyond.