Metal Separation Technology: What Works Best?
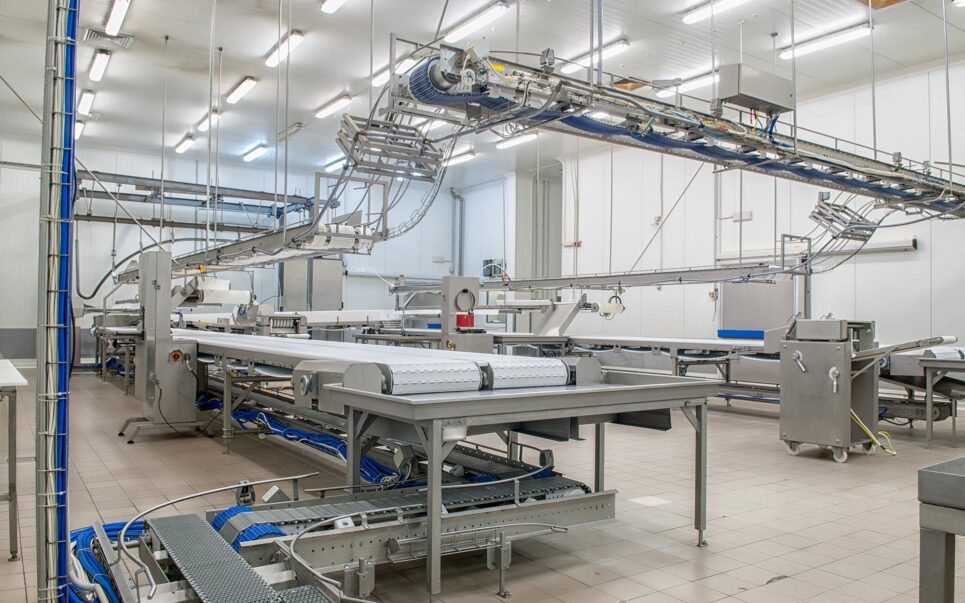
Metal separators, or magnetic separators, are the perfect solution to reducing metal contamination in final products. This type of equipment operates by exploiting the distinct physical properties of metals, such as magnetic susceptibility.
Magnets serve as the foundation of this process, exerting a magnetic field to capture metals, ensuring the purity and recyclability of countless materials.
The Role of Metal Detection and Removal in Food Processing
Metal detection and removal stand as guardians of food safety, diligently screening products for metallic contaminants that might pose a threat to consumer health. The food industry extensively deploys metal detection and removal equipment to maintain compliance with global food safety standards like the Hazard Analysis and Critical Control Points (HACCP) and to meet consumer expectations of product integrity.
Importance of Metal Detection for Food Safety
The presence of metal fragments in food products can lead to serious health risks, including injury or even death. Consequently, manufacturers prioritize metal detection and removal to intercept and eliminate these hazards before products reach the marketplace, safeguarding public health and upholding brand reputation.
Types of Metal Detection Equipment Used in the Industry
- High-frequency digital metal detectors excel in identifying both ferrous and non-ferrous metals concealed within food products.
- Gravity fall systems intercept metallic particles in powdered and granular products.
- Conveyor-based metal detectors, seamlessly integrated into production lines, inspect packaged and unpackaged items alike.
- Metal detectors with multi-spectrum technology, provide enhanced detection capabilities and minimize false rejects.
How Magnetic Separation Ensures Product Purity in Food Processing
Magnetic separation serves a dual purpose: extending the life of other processing equipment by protecting it from metal damage and ensuring product purity by removing ferromagnetic materials such as iron and steel from food products. Stainless steel, if it is work-hardened, can also be removed from processing lines using magnetic separators.
This preparatory step augments the effectiveness of subsequent metal detection processes and is an integral part of the quality assurance protocols in food processing operations.
Magnetic Separation: A Closer Look
Diving into the principle of magnetic separation reveals a fundamental process where magnetic forces isolate metals from other materials. Essentially, this process exploits the differences in magnetic properties between various metal types and non-metallic substances, resulting in the segregation of magnetic material.
Key Components Involved in Magnetic Separators
Diverse design configurations exist, yet a typical magnetic separator for food processing will include a magnet installed within a stainless steel housing.
Advancements in magnetic separation technology have come a long way, largely driven by increasing demands for product purity and efficiency. Innovations include the development of stronger magnetic materials, which has led to enhanced capture abilities, as well as modular designs that improve maintenance and operational flexibility.
Magnetic separators now integrate with sophisticated monitoring systems capable of signaling performance variations. Such technological improvements ensure high-quality separation that meets stringent industry standards.
Food-safe magnets are an exceptional tool for separating metals from food processing operations. Explore the types and benefits of these magnets for your company here.
Exploring the Diverse Industrial Applications of Metal Separators
Metal separators are integrated into numerous sectors, each leveraging these systems to maintain product quality, equipment safety, and operational efficiency. Below, discover how these devices are utilized across various industries and witness the transformative results of their application.
Widespread Deployment Across Industries
Food production facilities routinely install metal separators to detect and remove contaminants, thereby safeguarding consumer health and adhering to stringent regulations. Pharmaceutical manufacturers equally depend on these systems to ensure the purity of drugs, where even minuscule metal particles can have grave implications. Similarly, textile producers employ metal separators to prevent damage to machinery from needles or pins, which can result in costly downtime and repairs. Magnetic separators are also utilized across various industries, such as mining, rock crushing, agriculture, and more.
Innovations in Magnetic Separator Technology
Magnetic separators have undergone transformational developments in recent years. These advancements have significantly bolstered their effectiveness in removing unwanted metal contaminants. In food processing, in particular, high-gradient magnet systems have become increasingly prevalent due to their ability to capture finer, weakly magnetic particles.
Technological Advancements Enhancing Metal Separation
In the pursuit of optimizing metal separation, technologists have unveiled magnetic separators that are both more powerful and more selective. A notable improvement is in the design of magnetic separators, which incorporate rare-earth magnets. These offer a formidable increase in magnetic field gradient, ensuring even the smallest magnetic particles are captured with high precision. Some magnetic separators are equipped with sophisticated features such as self-cleaning mechanisms, which reduce downtime and enhance operational efficiency.
Complementing Technologies in Metal Separation
While magnetic separators excel at removing ferromagnetic materials, they constitute one aspect of an overarching metal separation strategy. Metal detectors and X-ray systems, which do not possess separation capabilities akin to magnetic separators, play a complementary role. Typically positioned after magnetic separation stages, these detectors provide an additional safeguard, identifying and flagging non-magnetic metals and other contaminants for removal.
- Advances in metal detection include greater sensitivity to a wider range of metal types, including non-ferrous and stainless steel.
- X-ray technology can detect non-metallic contaminants, further enhancing product safety and purity.
Combining magnetic separators with these technologies allows for a comprehensive approach to contaminant removal. This multi-layered defense is critical in food processing, where product safety is imperative.
It’s well known that both metal detectors and magnets have limitations – this is why, wherever possible, high-intensity compliant magnets and up-to-date metal detection technology combined are needed if the most responsible path of metal contamination risk reduction is to be pursued.
Find the Magnetic Separation Equipment You’ve Been Needing With Magnattack
Our array of food processing magnetic separation equipment can help your company create a safe and quality final product. By properly placing and validating your new magnetic equipment, you can rest assured they are as efficient as possible. Contact us today for a free consultation to see which equipment is right for you.