The Importance of Enhancing Efficiency In Food Processing Magnets
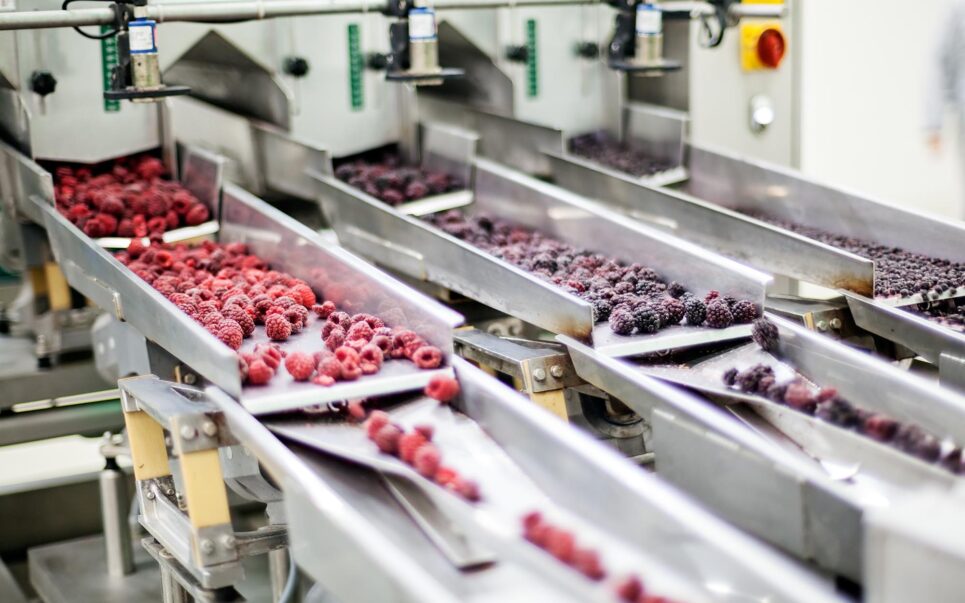
Creating your brand and company reputation takes time. With properly validated food processing magnets, your business can continue to create quality products while maintaining efficiency and safety.
Maintain Product Quality With Magnetic Solutions
Ensuring product purity is critical in food processing. Among the safety challenges, metal contamination stands out as a particularly insidious risk, potentially jeopardizing consumer health, tarnishing brand reputations, and provoking costly recalls. Contaminants can occur in various forms, including ferrous and non-ferrous metals, which, if undetected, can enter the food supply chain, posing significant safety hazards.
Given these consequences, the food industry continuously seeks advanced solutions to detect and eliminate these unwanted infiltrators. Enter food processing magnets: a frontline defense against metallic contaminants. However, their efficiency is not a set-and-forget matter—rigorous and regular magnet validation is crucial to maintain these systems’ protective vigilance.
The Consequences of Improperly Working Magnets in Food Processing
Magnetic separation is a critical control point in ensuring food safety. But what happens when food processing magnets are not functioning correctly? The implications can be far-reaching and damaging, both for consumers and producers alike.
The Impact on Final Product
When magnets fail to effectively attract metal contaminants, these impurities can end up in the final food product. Such oversights can compromise product quality, making the product unsafe for consumption and potentially resulting in a costly product recall. Moreover, even tiny metal particles in food can cause severe damage to processing equipment down the line, leading to downtime and repair expenses.
The Impact on Brand Reputation and Customer Satisfaction
Brand reputation is built on a foundation of trust and quality. If consumers discover that a food brand has allowed metal contamination to slip through the cracks, it can lead to widespread distrust. The negative press and word-of-mouth can result in diminished customer satisfaction, loss of loyal customers, and decreased sales and market share.
Worst Case Scenario Health Consequences
Health risks associated with metal contaminants in food range from minor to severe. In the most alarming cases, ingestion of metal pieces can lead to choking, injury to the mouth and internal organs, or infection. Such health hazards can not only result in legal consequences for the manufacturer but, in extreme situations, can also lead to severe or even fatal injuries for consumers.
The consequences of improperly working magnets extend far beyond a mere operational hiccup. They are central to maintaining food processing entities’ safety, integrity, and reputation. Comprehensive efforts must ensure magnetic separation systems always function at peak efficiency.
Looking at Magnet Validations
Magnet validations are critical measures taken to ensure the effectiveness and efficiency of food processing magnets. They confirm that the magnets are functioning optimally, which is crucial for maintaining the quality and safety of food products.
Improving Efficiency and Quality with Magnet Validations
The proper validation of magnets contributes significantly to the efficiency and quality control within food processing facilities. By regularly checking the strength and effectiveness of magnetic separators, facilities can help prevent potential contamination that could lead to costly product recalls and brand damage. Magnet validations also help identify any irregularities or decline in performance, enabling timely maintenance or replacement.
The Importance of Magnet Placement
Efficient magnet placement is as important as the magnets themselves. Strategic installation at critical control points within the production line ensures maximum protection against metal contamination. Placing magnets is pivotal in achieving a successful magnetic separation process, enhancing the overall efficiency of food processing operations.
Food Processing Magnet Validation Frequency and Process
Magnets should be validated regularly, with the frequency depending on the food processing environment and the magnet’s role within the facility. Typically, industry best practices recommend that validations occur annually. The validation process involves several steps:
- Inspecting the physical condition of the magnet.
- Testing the magnetic field strength to ensure it meets required standards.
- Checking for any material buildup that could inhibit performance.
- Reviewing the location and positioning to confirm optimal contaminant capture.
Once the validation is complete, detailed documentation should be provided. This documentation serves as a record for audits and helps in planning preventive maintenance schedules.
It is also important that plant operators regularly inspect and clean magnets. An overloaded magnet will not be as efficient, and foreign metal contaminants can remain in the product.
Are you looking for a proper magnet validation to be completed on your equipment? Magnattack® has top-notch assessment and validation services to keep your process efficient.
Magnattack Validations Help Improve Efficiency and Quality
The stringent standards in food safety and quality underscore the need for effective magnetic separation technology. Magnattack Global recognizes this imperative and offers a comprehensive range of validation procedures and risk assessments to ensure your magnets function optimally. Maximizing efficiency is crucial, but it must be paired with the unwavering reliability of equipment that comes into contact with food products.
Comprehensive Validation Procedures
Our validation process thoroughly analyzes your magnetic separators to verify their performance. We uncover any areas that may hinder peak efficiency by considering the product location and flow, assessing potential contaminant sources, and analyzing the material types being processed. This systematic approach allows us to address any challenges directly and implement solutions tailored to your specific operational needs.
Collaborative Risk Assessments
Understanding the risks in your food processing environment is pivotal. Our risk assessments are collaborative endeavors that involve aligning your operational objectives with magnet performance. This close collaboration ensures that your magnet solutions are optimally designed and positioned to prevent contamination risks and ensure the purity of your food products.
Tailored Magnet Solutions
We consider every detail of the application to ensure the magnets you receive are effective and the perfect fit for your production lines. By considering factors such as product flow, contaminant size, and material type, we can advise on your application’s most suitable magnet design and configuration.
- Thorough validation procedures to check magnet performance
- Risk assessments for improved safety and efficiency
- Individual consideration for product specifics
- Collaboration to customize magnets to application requirements
Enhancing efficiency and uplifting quality in your food processing facility starts with precise magnet validation and expert consultation. Discover the difference that Magnattack Global can make in safeguarding your products while bolstering productivity.
Feel Confident About Your Final Product With the Help of Magnattack Global
When it comes to food processing, don’t just leave things up to chance. Create an individualized solution to metal contamination in your processing line. Our professional services can keep you confident that you are producing quality final products that you can be proud of. Contact us today for a consultation.