Explaining Magnet Validation Procedures
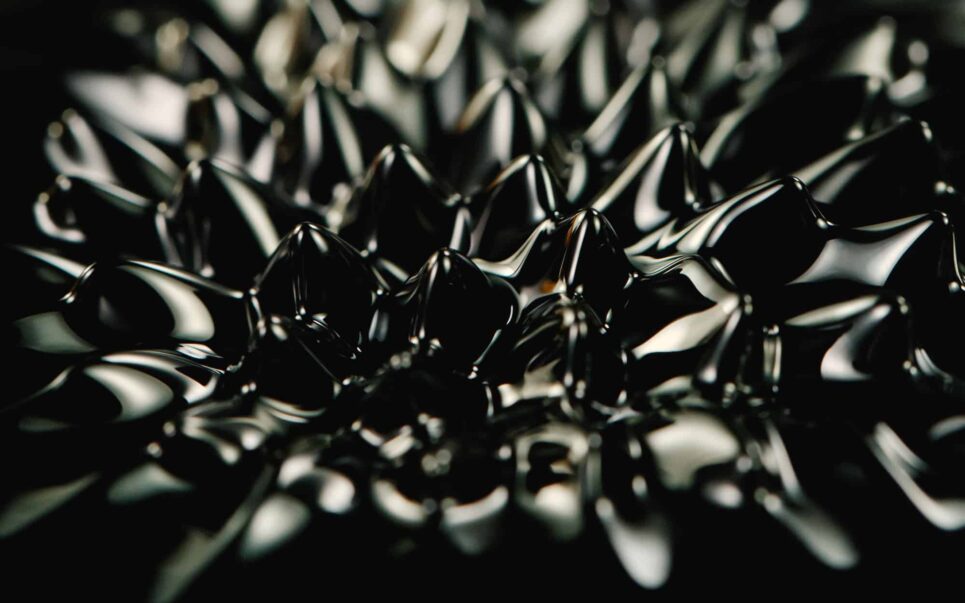
Insufficient metal fragment controls leave your company at risk of contamination, consumer complaints, recalls, financial loss, and legal implications.
In this blog, we’ll cover the following topics related to magnet validation procedures:
- What’s Included in the Magnet Validation Process?
- Factors That Impact Magnet Strength Measurements
- What Types of Magnets Need Validation Testing?
- Different Types of Magnet Validation Procedures
What’s Included in the Magnet Validation Process?
Most effective and professional magnet validations that can be relied on, involve an experienced technician visiting your food processing facility and conducting magnet strength testing using a calibrated Gauss meter. Additionally, the technician will inspect your magnets to ensure they are adequate for duty, and confirm that they’re designed based on industry standards and specified strength. Some of the factors considered are condition, safety, product stream coverage, retention, installation, type of magnet, and more.
With the right magnet validation process, you can:
- Reduce risks of metal contamination in your final product
- Obtain expert advice on protecting sensitive processing equipment from metal contamination damage
- Reduce the risk of consumer complaints, brand name damage, food recalls, and financial loss
- Prepare for upcoming plant audits and inspections
- Comply with stringent QA and industry standards
- Get valuable insights into the effectiveness of your existing magnetic separators and actions you can take to improve your foreign metal controls
Factors That Impact Magnet Strength Measurements
It would be ideal if magnets could retain their strength indefinitely. Unfortunately, that’s not the case. Magnets slowly reduce in strength over time, but there are several different factors that can further, and more rapidly, accelerate a magnet’s loss of strength and affect the lifespan and performance of your magnets, including:
High Temperatures
First and foremost, exposing magnets to temperatures outside of their design range can result in loss of strength. As a general rule of thumb, most standard Rare Earth (RE) magnets can withstand temperatures up to around 170 degrees Fahrenheit, after that, performance tends to decline. It’s important that when installing a magnetic separator in a high-temperature product line, you ensure to select a magnet that is designed and constructed with the correct grade of magnet material to withstand the heat.
Thermal shock is another common cause of demagnetization. An example of how this can occur is removing a magnet from a hot product and submerging it in cold water for cleaning.
Equipment Proximity
The machinery used near—or in conjunction with—your magnetic separation equipment can also affect its performance. For example, welding equipment used in close proximity to permanent magnets can damage the magnetic field, causing rapid strength loss.
Leaks
Where liquids are involved, breaches to the magnet’s enclosure will degrade the core magnet element which results in a reduction of strength. However, if the magnet design is such that the magnet circuit and magnet grade are correctly protected so that this issue is avoided, magnet strength loss is less likely to occur. Low-cost raw magnet elements are most at risk.
Physical Shock & Resonant Vibration
Mishandling is one of the most common culprits of a decrease in magnet strength. Magnetic separators are delicate systems, and rough handling often leads to a shorter lifespan and damage such as swelling, dents, and even exposed magnetic elements, which is very dangerous for product safety.
Abrasion
Abrasive products constantly impinging on the magnet surface will eventually lead to exposed elements or severe breakage. A magnet will wear more quickly in an abrasive product stream, such as corn, seed, cereal, or grain. For these types of applications, it is a great idea to consider durable magnet designs, such as the Magnattack® magnetic separators with Dura-Silk® abrasion reduction technology.
With even more other factors affecting magnet strength, it is very important to ensure proper handling when working with or around magnetic separation equipment. Once a magnet’s strength is lost, it cannot be ‘recharged’, so it is important to invest in quality equipment and handle it with care. So, how can you identify the current status of your equipment? Well, it’s simple. By conducting a proper magnet validation.
What Types of Magnets Need Validation Testing?
Generally speaking, any permanent final magnets used in the process flow of a food manufacturing facility should be subjected to annual validation testing. In addition, magnets on intake areas where supplier quality needs to be monitored and controlled should have the same standard as final magnets applied – for example, flour intakes in major bakery facilities. These assessments are aligned with industry-specific magnet standards, and apply to the following types of equipment examples:
Magnetic Plates
Mainly used to protect against medium and small-size contaminants, magnetic plates are typically installed in chutes, spouts, ducts, and over non-magnetic conveyors and screens.
Magnetic Grates / Drawer Magnets
These magnets found their niche removing fine, smaller particles from dry and free-flowing products. Grate magnets are extremely versatile and fit a variety of applications with odd and irregular shapes, floor openings, and vertical chutes.
Grates in Housings
Similar to the above, magnetic grates installed in housings aim to remove ferrous particles from free-flowing dry products.
Magnetic Traps and Liquid Line Magnets
These magnets are installed in pumped products such as liquid, emulsion and slurry lines, as they help remove small particles of scale, oxides, and iron contaminants from products.
Pneumatic Line Magnets
These magnets are used to collect contaminants from high-velocity flow pneumatic transfer lines, where retention of collected metals can be a challenge.
Bar Magnets
These magnets can be installed at the point of discharge on conveyor belts.
Poorly designed magnetic separators can have a negative effect on line pressure. Read how Magnattack overcomes this with our magnet designs.
Different Types of Magnet Validation Procedures
Food processing companies, magnet manufacturers, and magnet validation specialists have been debating the best way to test magnetic separators for a long time. While some argue that pull testing is the more effective method, others believe that Gauss testing is a more accurate and reliable method to test magnets.
Gauss Testing
With a gaussmeter, you can easily measure the magnetic flux density, also known as magnetic induction or magnetic field. Just place the Gaussmeter probe on the magnet’s surface and move it towards the high-strength pole until you get the peak high Gauss reading on the screen.
Pull Testing
Pull testing, on the other hand, involves using a small steel test ball placed on the magnet’s surface and then pulled off by the operator. The force required to do so is measured, giving you an indication of the magnet’s hold strength or holding force.
Both magnet validation procedures are quick and easy to perform, and for more accurate results, should be repeated multiple (5+) times and then averaged.
Regarding the question of which method is more effective and reliable, we have an answer backed up by years of research, experience, and discussion with industry professionals and food safety boards such as HACCP International:
The most effective and accurate method of testing magnet strength is with a calibrated gauss meter.
The main reasons behind this are that the figures for Gauss and pull test confirm that pull in ounces is not an SI value, meaning there is not an equivalent ratio between Gauss flux density and ounce pull over a variety of magnets.
Additionally, the Food Safety Standard 0909MAGSEP 1-2010 for final magnets in a food-related process correctly specifies final magnets should be a minimum of 10,000 gauss at 22 mm pole centers. For example, 10% more in pull test value with longer or wider pole centers may mean 20-30% less separating efficiency –a maximum of 22mm pole centers for final magnets at a minimum of 10,000 gauss on supply should be specified.
The most efficient magnet grate tube or bar for separating fine and weakly magnetic contamination is not the magnet showing the highest pull test value. The most efficient magnet will have the highest gauss at the shortest distance between pole band centers.
It is for these reasons that pull tests are not allowed in the current MAGSEP Standard as the basis for certified magnet validations on final packing or out loading magnets.
Key Takeaways
Like metal detectors and x-ray equipment, magnets are essential for ensuring food safety and preventing contamination during food processing. That’s why Magnattack® Global has teamed up with Active Magnetics Research (AMR) to offer HACCP-certified magnet validations. AMR are expert in coordinating magnet validation reporting for the food industry worldwide and has extensive experience in testing and analyzing metal fragment control systems.
By partnering with AMR, Magnattack® Global ensures that their magnet designs provide highly effective separation and retention efficiency for maximum food safety. When you partner with us, you can trust that Magnattack® Global and AMR are committed to protecting your final product from foreign metal contaminants. Contact us today for comprehensive insights on your existing magnets’ true effectiveness.