The Harmful Consequences if Magnetic Separators Aren’t Up to Standards and Compliance
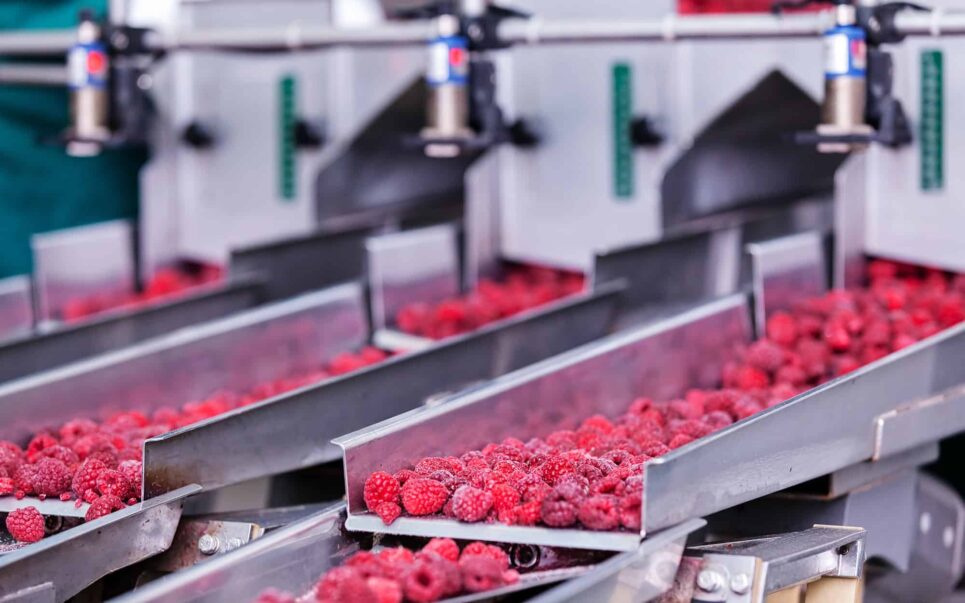
When magnetic separators aren’t up to par, there’s an increased risk of contamination. This can lead to a range of issues, from compromised product quality to safety hazards for consumers.
Read on to learn more about what can happen if your magnetic separators aren’t up to compliance standards.
The Importance of Magnetic Separators to Global Industries
Magnetic separators play a pivotal role across many global industries, such as baking, food processing, pet food, meat rendering, dairy, and more. In the magnetic separation process, magnetic separators serve as a vital control point in removing metal contaminants from diverse product streams. They thereby improve and increase the purity and safety of products, and can also protect expensive processing machinery from damage caused by metal contamination.
Roles and Functions of Magnetic Separators
At the heart of the magnetic separation process are the magnetic separators. They generate a magnetic field, which attracts and collects magnetic materials from the product, while non-magnetic materials travel around the magnet. This qualitative mode of separating magnetic particles has a significant relevance in many different industries like food processing, pet food, meat rendering, milling, as well as non-food industries such as mining, rock crushing, and many more.
Magnetic separators can also be used for machine protection purposes, to protect expensive processing machinery and equipment from potential damage caused by metal fragments in the product stream. This protective role extends to the products as well, by improving product purity, consistency, and meeting industry quality standards.
The Standards and Compliance for Magnetic Separators
To perform effectively, magnetic separators need to adhere to certain standards and regulations. These standards help ensure that the installed equipment is compatible with the product and application and effectively in removing & retaining contaminants. Additionally, magnetic separators that comply with standards are not likely to pose risks that non-compliant magnets can, such as re-contamination risks. Non-adherence to these standards can result in harmful consequences, product recalls, and more.
The Basic Requirements and Regulations
Efficacy, design, and safety form the core of the basic requirements for magnetic separators. The efficacy is validated by a magnet validation process and comprises several factors including magnet strength, ease of cleaning, product stream coverage, retention, position and condition of magnet, and more. Adequate magnet design ensures maximum magnetic field intensity, product stream coverage, and optimum product flow.
The design of magnetic separators should also grant easy access for routine maintenance, cleaning and inspection.
How Do Magnetic Separators Meet Standards and Compliance?
Magnetic separators meet standards and compliance through their designs, coverage of the product stream, strength, placement in the processing plant, and much more. Determining whether magnetic separators meet the set standards and achieve compliance is accomplished through a multi-step magnet validation or magnet testing process, which includes testing a magnet against a calibrated gauss meter.The gauss testing determines the magnet strength as that is one of the factors which affects a magnet’s performance and ability to remove metal fragments from the product.
Besides gauss testing, continuous monitoring and frequent inspections and cleaning are part of the magnet validation procedures to ensure that the separators continue to meet the standards. Upon identifying any anomalies, immediate corrective measures should be taken to rectify the faults.
The Role of Regulatory Bodies in Maintaining Standards
Regulatory bodies play a crucial role in upholding the standards and compliances for magnetic separators. They create, enforce, and update the guidelines that define the manufacturing and operational parameters of these separators. Companies like Magnattack® are well-known for developing final magnets that comply with current regulations.
These bodies also carry out regular audits and inspections, providing certifications to separators that successfully pass the set standards. Moreover, they promote awareness and provide training on the safe operations and maintenance of magnetic separators.
Explore tips on how to choose the right magnetic separator to help prevent metal contamination in your food products.
Potential Consequences of Non-Compliant Magnetic Separator
Non-compliant or subpar magnetic separators present a myriad of potential dangers that can severely impact industrial processes and generate harmful consequences. Understanding these risks is crucial to mitigate them and ensure operations run smoothly.
Direct Consequences for Industrial Operations
The primary purpose of magnetic separators in industries is to collect and remove foreign metal contaminants from product flows. However, non-compliant separators may fail to effectively carry out this magnetic separation process, leading to a significant impact on the quality of the end products. This, in turn, can damage the reputation of a brand, result in product recalls, and even lead to legal issues.
For instance, in food processing, a substandard magnetic separator might not effectively remove metal contaminants, leading to the risk of end consumers ingesting hazardous materials. Such scenarios can lead to liability claims and can severely damage a company’s reputation.
The Economic Impact of Non-Compliant Magnetic Separators
Along with the repercussions on the quality of the end products, the use of non-compliant magnetic separators can have severe economic consequences. Product inadequacy, high recall costs, legal issues, and damage to brand reputation brought about by ineffective magnetic separation processes could lead to financial losses. These can pose a considerable financial strain and might eventually lead to bankruptcy of a company in severe cases.
Safety Risks Associated With Magnetic Separators
Safety risks are a grave concern associated with the use of magnetic separators. The magnetic field produced by these separators should remain within the safe range from other metal objects; otherwise, it could lead to accidents. Following top magnetic separator safety tips and maintaining a safe distance is crucial to protect workers from harm, especially for people with cardiac pacemakers.
Accidents and injuries lead to delays in production and increased downtime. Additionally, companies might be liable for injuries caused under occupational safety laws. This can result in enormous compensation payouts.
Key Takeaways
With Magnattack®, it’s easy to upgrade your magnets to ensure they’re up to current standards and compliance regulations.
Upgrade your magnets with Magnattack’s RE80® Retromag Kits. Whether you need to replace pot magnets, inline magnets, or strainer basket magnets, these kits offer a quick and easy solution with no installation costs. The main features of these kits include custom designs and measurements, as well as various magnet inserts to fit different models. You can also upgrade to the latest technology with RE80® magnets and ensure compliance with MAGSEP Standards. Contact Magnattack® today and take your magnetic separation to the next level.