Your Guide for Choosing the Right Magnetic Separator
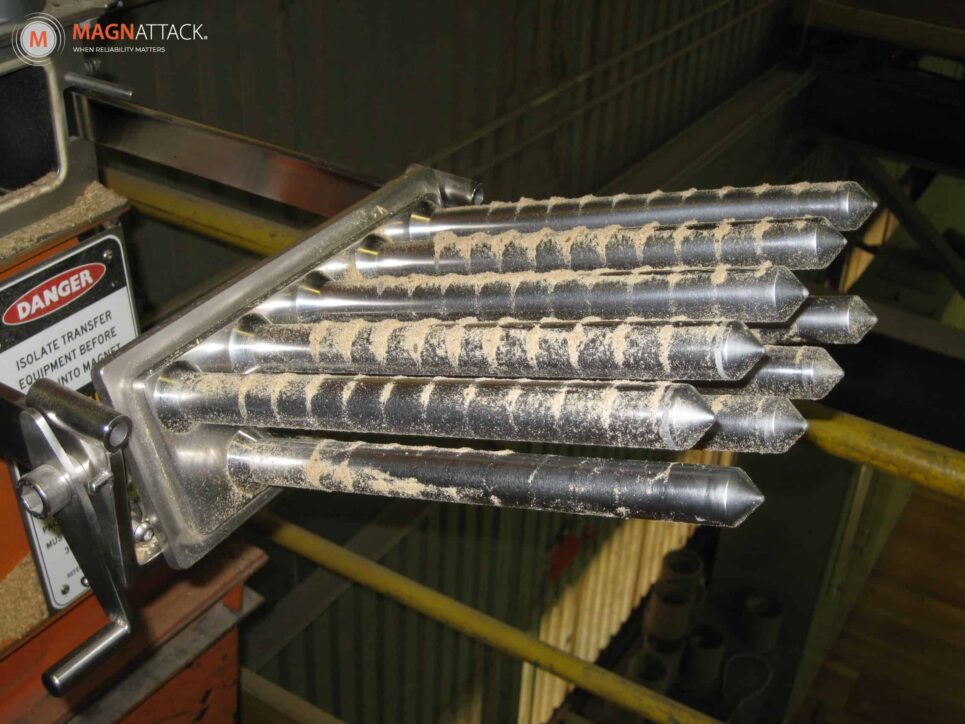
Magnetic separators are essential tools in many industries, from bakeries to food processing. Selecting the right one can make a big difference in efficiency and product quality.
So, what should you consider when choosing a magnetic separator? Read on to find out.
How Do Magnetic Separators Work?
Metal shards are known to enter the food supply chain at various points. This is a safety hazard because you don’t want people to ingest them, and they can also do damage to your production equipment. Magnetic separators are used to attract and remove metal contaminants from food products.
Magnetic separators are used in several different stages of the food production process, and they come in a variety of designs and sizes. They’re there to remove foreign metal contaminants from raw materials before processing, and metal from finished products before packaging and bulk loading.
How to Choose the Right Magnetic Separator
When it comes to finding the right magnetic separator for your needs, there are a few key factors to consider:
Process Feed Method
When considering which separator is right for your processing application, it’s important to think about how your product is being conveyed through the process. Is it gravity fed? Or maybe it’s being transported through a pneumatic system, a mechanical conveyor, or a pressure pipeline? Each conveying method has its own unique requirements, so the magnetic separator type will depend on the process feed method. An RE80® Separation Shaft will not provide proper product stream coverage (or be the correct design) for an application such as a high-velocity pneumatic line, so it is a good place to start with considering the process feed method first when selecting a magnetic separator.
Product Type and Consistency & Material Flow Characteristics
Consider the type and consistency of your product. Is it a dry and free-flowing powder, does it have issues with bridging, or is it moist or lumpy? Is it a liquid, or a slurry-type product? Each category requires a different approach. Whether it’s dry free-flowing goods, powders, pellets, granules, wet viscous solutions, or even slightly damp products prone to clustering or caking, the type of material you’re dealing with is key to choosing the right magnetic separator that matches your materials’ flow.
For dry and free-flowing powders, a magnetic separator such as a drawer magnet or a grate magnet can be a great choice for removing those unwanted metal particles. The Rapidclean® Drawer Magnet and Mag-Ram® Self-Cleaning Grate Magnet are both excellent choices for dry, powder product applications.
However, if your powder has bridging characteristics, you could potentially need a rotary magnetic separator, which will be able to break down lumps and eliminate the issue of bridging. Moist or lumpy powders, such as baby formula, need a separator that can handle their sticky texture, so a magnet such as the Rapiclean® Rotary Magnetic Separator is an effective choice for these applications.
When dealing with liquids, choosing a magnetic separator designed for liquid applications is essential. There are a number of important factors to consider, such as: is the magnet able to withstand both product and CIP temperatures? Can the magnet be safely removed for frequent cleaning, and can the magnet also be cleaned effectively without the use of unhygienic methods excluded in the current standards?
If the product is highly viscous, it needs to be designed to have the ability to collect and RETAIN the collected fragments.
Learn more about the Pressure Pipeline Separator and the Emulsion & Slurry Pipeline Separator.
Mag-Ram® Self-Cleaning Magnet
The Mag-Ram® is a self-cleaning magnetic separator that takes magnet cleaning to the next level. With its modular design, you can customize the Mag-Ram® to meet the demands of many dry product applications. You have the ability to choose the number of Magnet Rams and/or Rows that suit the requirements of your process and provide you with optimum protection.
Key features and benefits of the Mag-Ram® include:
- Large diameter that effectively captures and retains foreign metal fragments
- Pneumatic cylinders that ensure synchronized cleaning and prevent jamming issues
- Customized controls for automatic self-cleaning available, with options like timer controller or direct wire to PLC
- Operator safety with easy, quick, and safe metal fragment removal
- High-intensity magnets certified to 11,000+ gauss for superior strength and retention
- USDA Accepted
Process Flow Rate
Take into account the volume of product passing through your process. This is essential as it directly affects the design, size, and features of the metal separator. Whether you’re dealing with tons of product per hour or less, make sure you know your numbers. You want a separator that can collect and retain the metal contamination, and that can be cleaned frequently enough. The same concept applies to high-velocity lines, which require the magnetic separator to be able to cope with the high speed of the product and be able to retain the contamination.
Learn more about the Spherical Pneumatic Line Magnet and the Powder Transfer Magnet for high-velocity pneumatic applications.
Type and Volume of Metal Contamination
The type and volume of metal contamination should be considered when choosing a magnetic separator. If you’re dealing with larger pieces of tramp metal like nuts, bolts, or screws, then a magnetic separator designed for this type of contamination could be slightly different than a magnetic separator that targets fine metal particles, such as stainless steel. The difference could be in the spacing between magnet bars, as larger contaminants are picked up more easily than fine dust-like metal particles. When choosing a magnetic separator, also consider factors like the size of your operation, the material you’re processing, and your desired level of automation. The right magnetic separator can significantly improve the efficiency and productivity of your processes.
Cleaning Method
Choosing the right cleaning method is essential to ensure optimal performance and compatibility with your entire process. The cleaning method should be considered with the above point of the type and volume of metal contamination, as higher volumes of contaminants mean the magnet needs to be cleaned more frequently. Whether you’re dealing with powders, liquids, or any other materials, finding the perfect cleaning solution is a must. Understanding the intricacies of your specific process is key to selecting the best cleaning method for your magnetic separators. You don’t want to risk damaging your equipment or compromising the efficiency of the system, or allow the magnets to get overloaded and lack in their efficiency. So, how do you choose the right cleaning method? That’s where careful evaluation and expert advice come into play. By considering factors such as the type of separator, the materials being handled, and the level of contamination, you can make an informed decision.
The Mag-Ram® Automatic Self-Cleaning Magnet is an excellent choice for applications with high volume of contamination and high product tonnage rate. The Mag-Ram® can be programmed to clean during, before or after production runs, as well as clean one magnetic Ram at a time or all Rams simultaneously!
Spherical Pneumatic Line Magnet
The Spherical Pneumatic Line Magnet is a revolutionary magnetic separator that combines high-gauss magnetic strength with an advanced fragment retention design to effectively capture even the smallest metal fines and flakes in high-velocity, pneumatic powder applications. Key features include a bellied housing to minimize pressure change, positioning collar with key for correct magnet probe placement, and a tethered handle for operator safety. The aerodynamic magnet housing prevents product buildup and the Morris coupling ensures easy installation.
Operating Temperature
Different separators are designed to handle specific temperature ranges, and choosing the wrong one can lead to disappointing results. When a magnet loses strength, it is called demagnetization. This can occur due to thermal shock, which can happen when a magnet is pulled out of a hot product and submerged in cold water for cleaning. Demagnetization can also occur when a magnet that is not designed to withstand high temperatures is installed in a high-temp process.
By doing your research and selecting a separator that can withstand temperature extremes, you’ll be saving yourself from potential problems in the future.
From pneumatic transfer to gravity-fed applications, view Magnattack®’s wide range of dry magnetic separators.
Key Takeaways
Magnattack® understands the importance of keeping your food safe for consumers. We’ve provided food manufacturers with dependable solutions that bolster their approach to foreign metal control for over 50 years. Start a conversation with our expert team or schedule a free consultation to learn more.