How to Tell if Magnets Are Functioning at Their Best
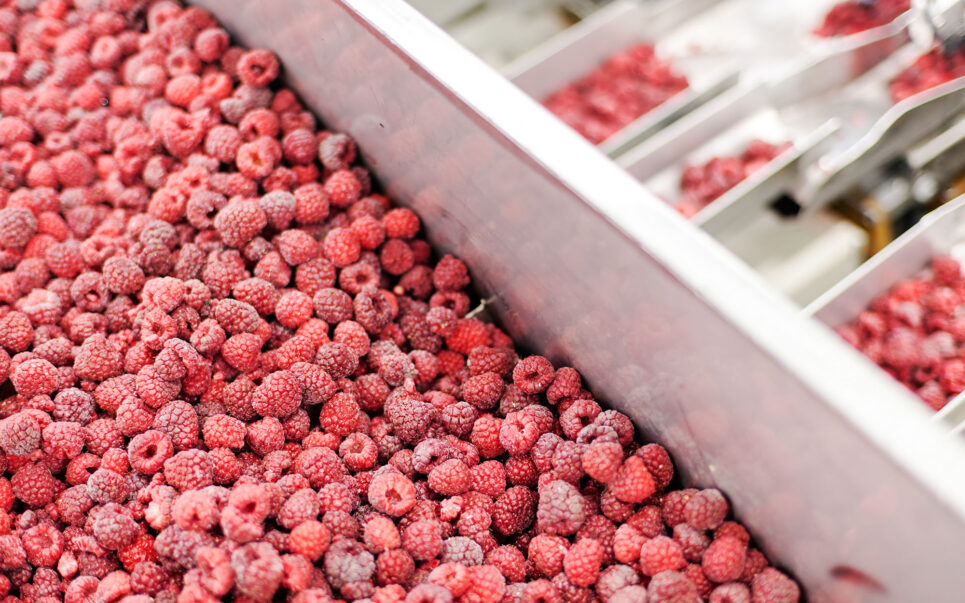
Ensuring your magnets are performing optimally is essential to maintaining safety and quality in food production. Magnetic separation equipment is a key tool in reducing the risk of metal contamination, but how do you know if it’s still doing its job effectively? This guide will help you understand the signs that your magnets might need attention, the importance of magnet validations, and how often inspections should be conducted.
How To Know If Magnetic Separation Equipment Isn’t Performing Right?
Magnetic separation equipment plays a crucial role in food safety by removing metal contaminants during the production process. However, over time, various factors can impact a magnet’s performance, making it less effective. Here are some key signs that your magnets might need attention:
Increased Contamination in Final Product
One of the most obvious signs that your magnets are underperforming is a noticeable increase in metal contaminants found in your products during post-production testing. If your magnetic separation equipment is no longer capturing as much metal as it used to, it could indicate that the magnet’s strength has weakened or that there’s a buildup of contaminants around the magnet affecting its performance. A decrease in metal capture efficiency could put your food products at risk of contamination, leading to recalls and product rejections.
Magnets Are Overloaded or Damaged
If your magnets are overloaded with fragments or damaged, their ability to collect and retain metal fragments can be significantly reduced. This means that an overloaded magnet is unable to collect any more metal fragments, and those contaminants will remain in the product. A damage to a magnet can lead to loss in strength, which can also result in less effective metal fragment control. Another sign may be an increase in metal detector rejections.
Magnet Validations
A magnet inspection is an effective way to determine whether your magnets are suitable for their intended function. If left unchecked, underperforming magnets can lead to higher contamination rates, exposing your business to significant risks, including potential food safety violations and damage to your reputation. Knowing the condition of your magnets allows for corrective actions to enhance inadequate metal fragment control.
Exploring Magnet Validations
Magnet validations are essential for ensuring that your equipment is functioning at peak efficiency. During a magnet validation, professionals assess the condition, strength, and overall effectiveness of the magnets. Here’s what’s involved:
Physical Inspection
A visual inspection of your magnetic equipment helps identify any signs of physical damage, wear, or buildup that may be impacting its efficiency. This step is crucial for understanding whether the magnet’s structural integrity has been compromised and whether it needs cleaning or replacement.
Magnet Strength Measurement
Magnet strength is one of the most important factors in determining how well a magnet performs. During the validation process, calibrated Gauss meters are used to measure the magnetic strength to ensure it meets the HACCP International Standard. Over time, magnets can demagnetize, which weakens their ability to capture contaminants. A strength measurement will help determine if your magnet is still fit for its application.
Risk Assessment
An experienced technician will assess the risks associated with the current magnet or the absence of a magnet in areas requiring metal fragment control. A risk assessment helps you determine whether your current magnet setup is adequate for the level of contamination in your production process or if upgrades or additions are necessary.
Compliance Verification
Validations also include checking for compliance with the HACCP food safety standard. It’s important that your magnets are certified and up to date with all necessary safety protocols to avoid costly non-compliance issues, such as product recalls. Upon purchase, new magnets should come with a certificate confirming their strength and compliance with standards such as HACCP International Food Safety Standard 0909MAGSEP 2-2021.
Are you aware of the consequences of not having up-to-standard equipment? Explore these potential effects in this informative guide.
How Often Should I Have My Magnets Inspected and Validated?
Maintaining your food processing magnets through regular inspections and validations is key to ensuring they continue to perform effectively. But how often should this be done?
Validation Schedule
A consistent schedule for magnet validations helps manage various risks related to factors such as production volume, contamination risks, and the type of equipment used. If your plant processes large quantities of ingredients, especially more abrasive kinds, the magnets may experience more wear and tear, therefore requiring more frequent validations or monitoring. These can be done in-house by quality personnel for additional food safety measures. However, annual validations by experts are crucial for receiving reliable guidance on the overall effectiveness of your metal fragment controls.
General Guidelines for Inspections
As an industry best practice and as documented in the 0909MAGSEP 2-2021 Magnet Standard, it is recommended that magnets be inspected and validated annually to keep track of any deterioration and changes that can affect product security. In some high-risk environments, more frequent inspections may be valuable to detect deterioration early on. Some companies have chosen to conduct an external validation every six months to ensure they stay ahead of any potential magnet deterioration. After all, it’s a small price to pay – prevention is better than cure.
New Magnets and Calibration
New magnets should always come with certification confirming their strength and compliance with industry standards. Instruments used to test and validate magnets must be calibrated and traceable through relevant authorities to ensure the data collected is accurate and reliable.
Who Can Perform Magnet Validations and Inspections?
When it comes to ensuring your food processing magnets are functioning properly, it’s essential to partner with professionals who have the experience and qualifications necessary to perform thorough inspections and validations.
Certified Food Industry Professionals
Certified professionals with expertise in the food industry should conduct magnet validations. They will provide accurate risk assessments, strength measurements, and compliance checks to ensure your magnets meet food safety regulations. By partnering with an experienced provider, you can avoid the risk of inaccurate readings or overlooked issues.
Importance of HACCP and Other Certifications
Certifications such as HACCP and USDA are strong indicators that a magnet is designed to meet stringent food safety standards. These certifications ensure that the magnet is safe, sanitary, and suitable for food processing applications.
AMR Consulting, in partnership with Magnattack® Global, offers comprehensive magnet validation services. Their team provides certified HACCP International reports, risk assessments, and accurate testing to ensure your magnets meet current food safety requirements. If you’re concerned about your magnets’ performance, reach out to Magnattack® Global for expert assistance.
Validate Your Magnetic Equipment With AMR Consulting and Magnattack
Partner with AMR Consulting and Magnattack to ensure your food processing magnets are performing at their best. With certified HACCP validations, comprehensive risk assessments, and detailed magnet testing, you can maintain compliance with food safety standards and reduce contamination risks. Contact Magnattack today to schedule a professional validation and protect the integrity of your food production process.