How to Help Avoid Recalls in Pet Food Processing
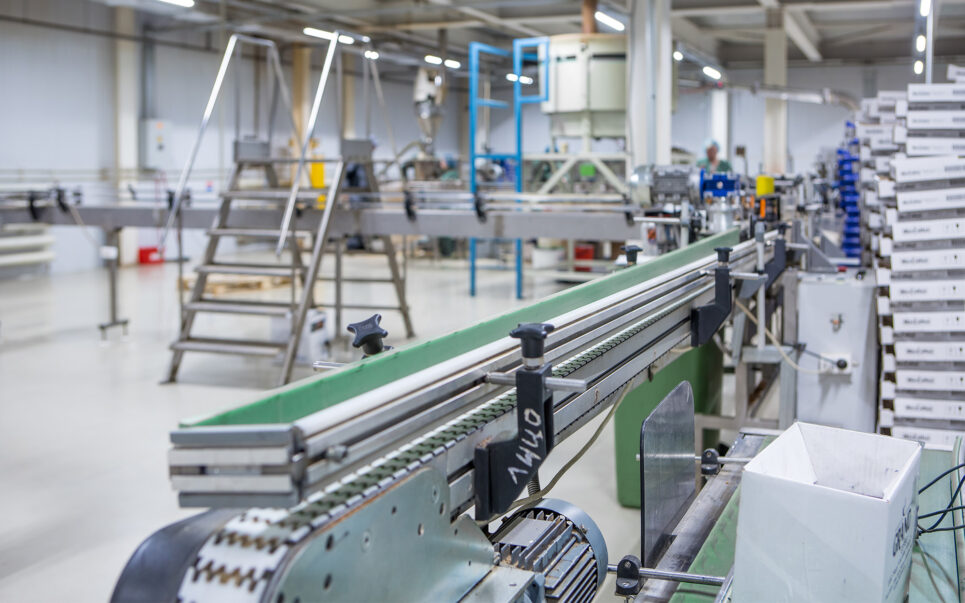
For those in the pet food industry, vigilance against contamination is a constant concern. The complexity of processing, from ingredient handling to packaging, presents numerous points where foreign materials can enter the production line.
Ensuring Safety and Quality From Feed to Food
The journey from raw feed ingredients to the high-quality pet food that finds its way into the bowls of our furry friends is underpinned by stringent safety and quality measures. Implementing robust food safety protocols is pivotal in pet food manufacturing processes, ensuring that the end products are not only nutritious but also safe for pet consumption. These measures are essential for maintaining the trust of pet owners and protecting the health of their pets.
Why Food Safety Is Critical in Pet Food Manufacturing
Recalls in the pet food industry are not only costly from a financial perspective but also damaging to brand reputation and consumer trust. A single recall incident can impose a significant burden on a production plant, both in terms of product losses and the potential impact on the company’s image, not to mention huge potential financial losses. It is critical for manufacturers to realize this risk and have comprehensive quality control measures in place.
Minimizing Risks With Magnetic Separation Technology
One such technological advancement in the realm of safety measures is the use of magnetic separators. These devices are crucial in the early detection and minimization of metal contaminants which, if left unchecked and remaining in the product, can lead to product recalls. The strategic placement of magnetic separators within the processing line, as well as the diligent maintenance of magnets, significantly reduces the risk of contamination in the final product. By ensuring these protocols are followed, pet food manufacturers can maintain a continuous line of defense against potential recalls, safeguarding not only the animals’ health but also the brand’s integrity and financial viability.
Maintaining Consistency in Safety and Quality
The commitment to safety and quality in the pet food industry is a continuous process. From sourcing reliable ingredients to employing advanced technologies like magnetic separators, every step is vital in producing pet food that is safe, nutritious, and enjoyable for pets. As the industry evolves, so too must the methods and approaches to ensuring that our pets’ food remains of the highest standard.
Common Reasons for Recall in Diverse Pet Food Types
Ensuring the safety of pet food is crucial for the health of pets and the ease of mind for their owners. Despite rigorous standards, recalls are sometimes necessary to prevent risks. Each type of pet food, whether dry, wet, treats, or raw, has unique processing techniques that can be susceptible to different issues resulting in recalls.
Why Different Pet Foods Face Recalls
Dry pet food, typically processed through extrusion, can face recalls due to contamination with bacteria such as Salmonella or due to the presence of foreign materials. Additionally, incorrect levels of certain nutrients can lead to a recall if they pose a health risk.
Wet pet food is prone to spoilage if not properly sealed or if the food undergoes an inadequate sterilization process. Additionally, similarly to dry food, contamination with pathogens and foreign materials, or incorrect nutrient levels can also lead to recalls.
A common issue between the two different types of pet food processing methods is the risk of metal contamination. Both production lines are susceptible to this kind of compromise and should be handled with consideration of this in mind.
The Link Between Formulation and Safety
Different pet foods are formulated with specific dietary needs in mind. However, ensuring the safe production of these ingredients is paramount. Any slip-up in the meticulous balance of formulating pet foods can lead to deficiencies or toxicities, resulting in recalls and, more importantly, health issues for animals.
- Dry Pet Food: Balancing the consistency and shelf-life without compromising nutrient content
- Wet Pet Food: Maintaining the correct moisture levels while preventing microbial growth
The health of pets is intricately linked to the quality of their diet. A safe and carefully monitored production process translates into wholesome, dependable meals that pet owners can trust. Understanding these common recall reasons helps manufacturers refine their safety protocols and protect both pets and their owners.
Cutting-Edge Solutions in Pet Food Processing
In an industry where the margin for error is slim and the cost of failure is high, no business can afford the financial backlash and reputational damage that comes with a product recall. As a manufacturer, your goal is to produce pet food that is not only nutritious and appealing to pets but also safe from possible contamination that could trigger harm or a costly recall. By focusing on the critical aspects of pet food processing, businesses can better safeguard their operations, protect their brand, and keep the well-being of their four-legged consumers at top of mind.
Awareness and proactiveness are crucial in avoiding recalls that can result from such contamination. At Magnattack®, we understand the intricacies of both dry and wet pet food processing and have developed targeted solutions to help secure the safety and integrity of your products.
Wet and Dry Solutions for Pet Food Processing Plants
When it comes to safeguarding your operations against contaminants, knowing the right solutions that cater to both wet and dry applications is vital. For dry pet food applications, the Magnattack range includes state-of-the-art separators such as the Mag-Ram® Self-Cleaning Magnet and Rapidclean® Drawer Magnet, designed for quick and effective metal fragment control. These systems are highly efficient, reducing the risk of contaminants making their way into the final product, thus enhancing your preventive measures against recalls.
Other dry product solutions include the Spherical Pneumatic Transfer Magnet for pneumatically conveyed powders, grains, premixes and palatants, as well as the Bullnose Plate Magnet, designed for applications such as processing of chicken frames, whole muscle products, poultry, beef, lamb, venison, etc., prior to expensive processing machinery such as grinders, shredders, dicers, and emulsifiers.
Safety measures differ in wet pet food applications due to the nature of the product and processing equipment. Solutions such as the Emulsion and Slurry Pipeline Separator and Pressure Pipeline Separator can be integrated into the system, ensuring that metal fragments are captured even in a viscous product stream. This is just one example of how protective measures can be tailored to different production environments within the pet food industry.
Each Magnattack equipment model, from high-intensity separators to self-cleaning systems, is engineered with a deep understanding of the pet food processing industry’s specific challenges and regulatory requirements. Implementing these solutions not only proactively steps towards preventing costly recalls but also helps businesses striving for a high-quality nutritious product.
Maintain Your Pet Food Processing Brand and Partner With a Reliable Magnetic Separator Company
Magnattack is here to help with your wet and dry pet food processing. Our range of magnetic separators and technicians’ expertise can bolster your safety measures and give you peace of mind. Contact us today for a consultation.