What’s the Best Location for Magnet Separators in My Pet Food Plant?
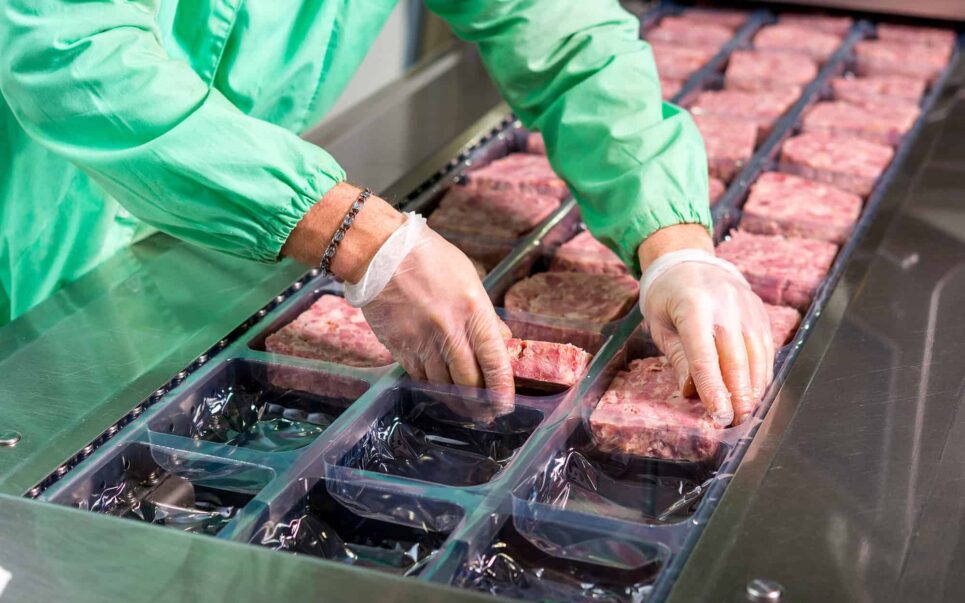
Did you know that metal contamination is a serious concern when it comes to pet food production? In fact, studies have shown that a staggering 65% of food processors experience some form of metal contamination in their pet food products.
While many processors are aware of the need for magnetic separators to increase food safety, there’s often confusion when it comes to the proper positioning of this equipment. Think product recalls, damaged reputation, and potential harm to your customer’s beloved pets—that’s definitely not what any pet food business wants!
But fear not, because there’s an easy and affordable solution. In this blog, we’ll guide you along the way toward achieving optimal product-to-magnet contact and ensuring the highest level of safety for your pet food products. Keep reading to discover practical applications, insights, and recommendations from professionals who’ve mastered the art of magnetic separator placement.
Your Guide to Optimal Product-to-Magnet Contact: Understanding Where Metal Separators Are Most Effective
Strategically placed magnetic separators are essential to the safety and quality of pet food processing. Here’s four optimal locations to install this equipment:
1. Infeed Material
First things first, let’s start with receiving and processing raw materials. Installing magnetic separators at the infeed material stage—for both dry and wet ingredients applications—is crucial for effective metal separation. Here’s what magnet types work best for these particular locations:
What Magnetic Separators Handle Infeed Material the Best?
- Dry Ingredients: Spherical Pneumatic Transfer Magnet – For dry ingredients, the Spherical Pneumatic Transfer Magnet is perfect for pet food applications involving powders, grains, premixes, and palatants that are pneumatically conveyed. These magnetic separators offer an aerodynamic design, so there are no sharp edges to disrupt the material flow or cause pressure changes. Simply put, it keeps your production line running smoothly by preventing product build-up and ensuring top-notch performance.
- The Mag-Ram® Automatic Self – Cleaning Magnet is designed to handle incoming raw materials—like grain, protein meal, and meat and bone meal (MBM)—right before the bagging stage. With automatic self-cleaning capabilities, it quickly and efficiently removes ferrous metal contaminants while offering unparalleled performance, reduced downtime, and maximum output and profitability. Even better, with dedicated contaminant chutes and pneumatic cylinders for individual control, it’s never been easier to maintain the purity of your pet food products.
- Wet Ingredients: Bullnose Plate Magnet – Now, let’s move on to the wet applications. The Bullnose Plate Magnetic Separator is a star player when it comes to safeguarding meat-based pet food products. Often installed before expensive processing machinery like grinders, shredders, dicers, and emulsifiers; this magnet is specially designed to capture and remove metal contaminants from applications such as chicken frames, whole muscle products, poultry, beef, and more. With the Bullnose Plate Magnet in place, you can rest easy knowing that the integrity of your product is protected.
2. After First Stage Mixing / Wet Ingredients Processing
Once your products pass through the initial mixing phase, it’s time to ensure that any metal contaminants introduced into your product during processing can be extracted. Installing magnetic separators right after this stage adds an extra layer of protection, and can relieve the burden on your final magnets, especially if your metal contamination levels are high. There is a magnetic separator perfectly equipped for this application.
Which Magnetic Separator is Most Effective After First Stage Mixing?
For viscous applications like meat emulsions and slurries, look no further than the Emulsion & Slurry Pipeline Separator with Acutex® Probes. Specifically designed to ensure the purity of your slurry mixtures, this magnet comes equipped with a coned body, which cleverly eliminates pooling areas and air pockets and guarantees a smooth flow of liquid products. Even better, it boasts an innovative design that strikes a balance between magnet strength and open space, enabling optimal product-to-magnet contact.
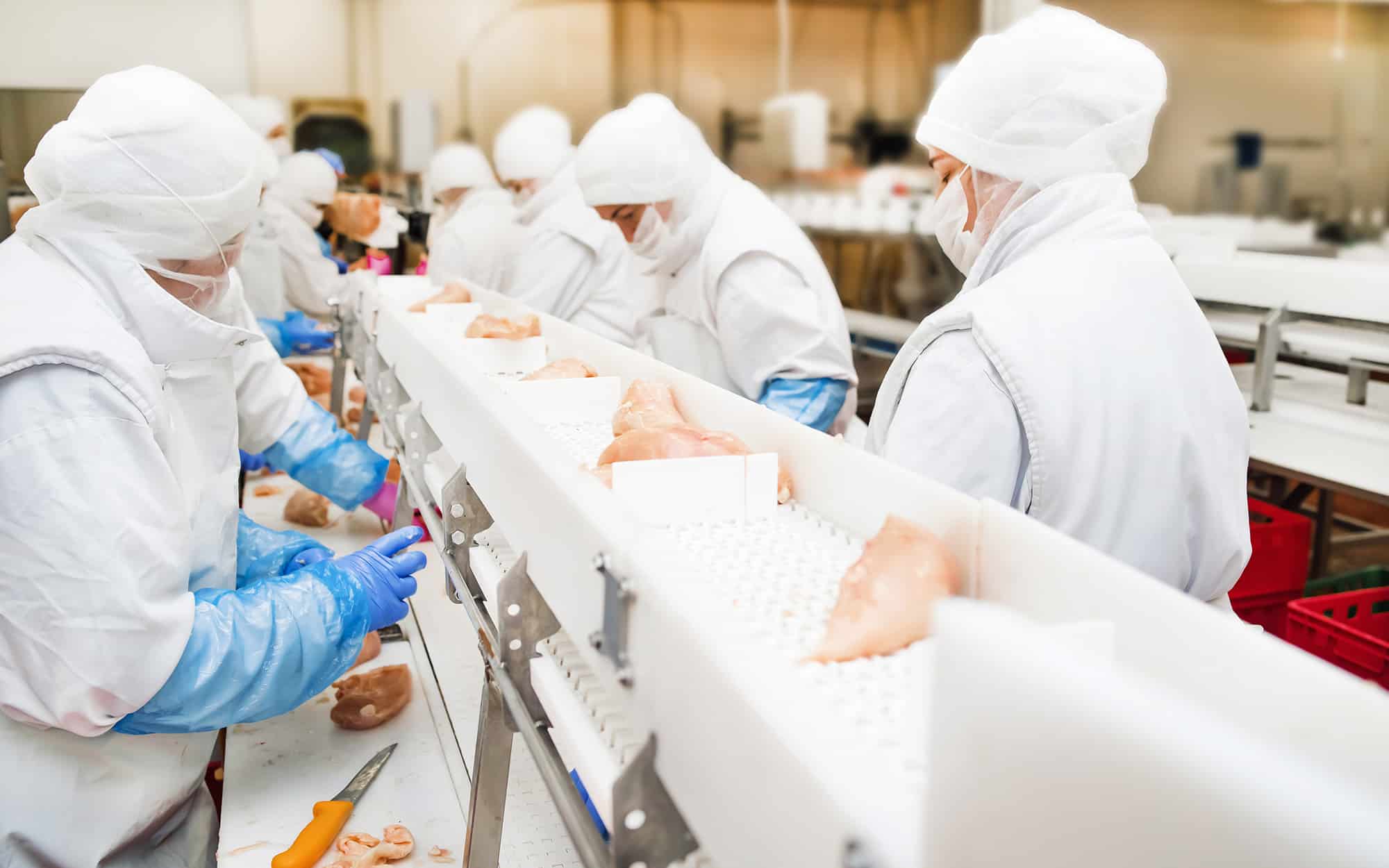
3. On the Wet Line Prior to Canning / Packing
For facilities involved in wet pet food production, magnetic separators play a crucial role in the canning process. Here’s what magnets work best for this duty as final controls: The Emulsion & Slurry Pipeline Separator and the Pressure Pipeline Separator. These magnets can be designed and configured to suit all types of wet products that are pumped to the filling machine. The flow rate, solids, particle size and viscosity need to be considered for a successful result. These magnets are essential for final control over the finished product prior to packing / metal detection and ultimately reaching the consumer. These magnets are often installed upstream of expensive pumping equipment (e.g. twin screw pumps) to effectively protect them from metal damage and this causing further contamination to the final product.
4. Dry Ingredients Processing
Magnetic separators for this location largely depend on the flow rate and what level of protection is necessary. It is important to ensure there is adequate control during processing to prevent contaminants being trapped in the finished kibble and be more difficult to separate. This means finding a suitable location prior to extrusion, where the product is conducive to separation, as this may yield a higher prevention than the final magnet on kibble. This alone will greatly reduce hits on your final product once it is turned into kibble and packed.
Which Magnetic Separators are Most Effective in Dry Ingredients Processing?
- The above-mentioned Mag-Ram® Automatic Self-Cleaning Magnet is a very effective solution for dry ingredients processing.
- Bullnose Plate Magnet – also mentioned above, the Bullnose Plate Magnet is another excellent choice for dry ingredients.
- RE80® Separation Shaft – This high-intensity magnetic separator is designed to split the flow of the product and maximize product-to-magnet contact. These magnets effectively extract splinters of stainless steel, magnetic stone fragments, and >98% of tramp iron and ferrous fines from dry products.
- The Rapidclean® Drawer Magnet: This solution is highly effective in handling dry ingredients like meals, powders, grains, and premixes. Equipped with large diameter RE80® magnet bars, this magnetic separator guarantees optimal retention of even the finest, weakly metal fragments. Simply put, it’s designed to collect and retain metallic particles from dry ingredients, no matter how tiny they might be.
Ensuring food safety isn’t simply a legal requirement—it’s a moral obligation. Check out our comprehensive list of magnetic separators revolutionizing the pet food industry, and a few reasons why you can’t afford to miss them.
5. On the Dry Line Prior to Bagging
The final magnet prior to bagging is crucial should an issue arise, which is why it is important to ensure that you have magnets that are certified and traceable. Doing so also allows you to demonstrate clear prevention measures prior to bagging.
When it comes to the dry line, it’s essential to control ferrous contaminants to an acceptable level and as per best practice prior to the bagging process. Essentially, this is the last line of defense before the product reaches the consumer, so let’s explore what type of magnetic separator is most effective when placed in this location.
Which Magnetic Separators are Most Effective on Dry Lines prior to Bagging?
Choosing a magnetic separator for these applications will depend on the flow rate, density, speed, and more. Magnetic separators suitable for these applications:
- The Mag-Ram® Automatic Self-Cleaning Magnet
- The Rapidclean® Drawer Magnet
- The Bullnose Plate Magnet
- The RE80® Separation Shaft
When Reliability Matters, Turn to Magnattack®
With over 50 years of experience in the food processing industry, Magnattack® offers a revolutionary way to approach foreign metal control. Thanks to our cutting-edge technology and commitment to excellence, we’ve built a reputation as a trusted provider for pet food facilities worldwide. Don’t compromise on the safety of your production process—explore our listing of metal separators for pet food applications today!