Magnetic Separation and the Food Industry: FAQs You Need to Know
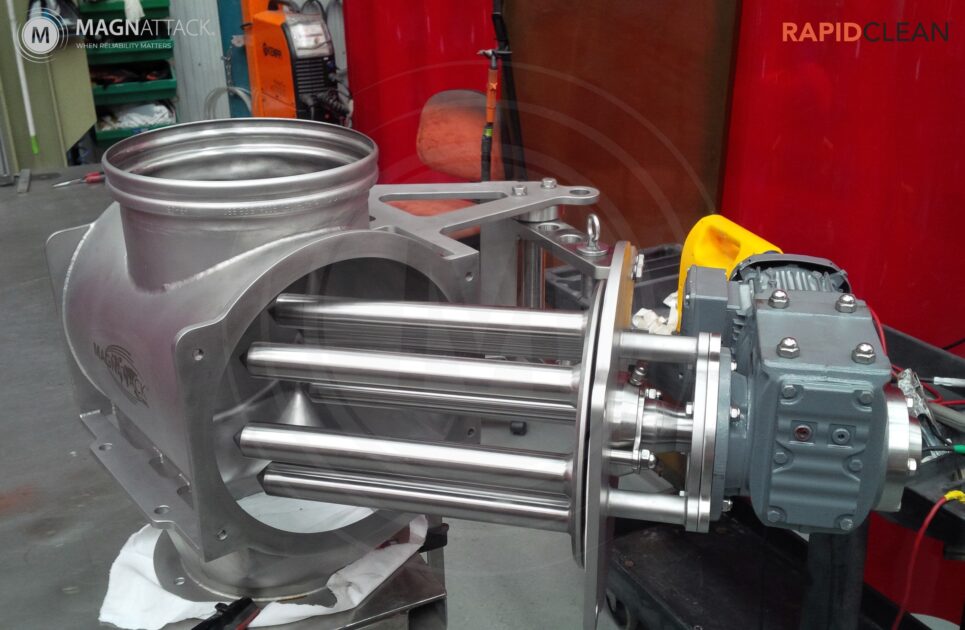
For businesses in the food industry, magnetic separation is the secret ingredient for a safe and pure supply chain. It’s critical to the production process because it removes metal contaminants from food products. But how does it actually work? More importantly, what equipment is best for your unique applications?
Keep reading to find out.
How Do Food Processing Magnets Work?
Metal shards are known to enter the food supply chain at various points. This is a safety hazard because you don’t want people to ingest them, and they can also do damage to your production equipment. Magnetic separators are used to attract and remove ferrous contaminants from food products.
Magnetic separators are used in several different stages of the food production process, and they come in a variety of designs and sizes. They’re there to remove contaminants from raw materials before processing and metal from finished products before packaging and bulk loading.
What Types of Magnetic Separation Equipment Are Used in the Food Industry?
There are several types of magnetic separation equipment commonly used in the food processing industry, including:
- Plate Magnets: These are flat magnetic plates most often seen in conveyor belts or chutes. They’re typically used to remove metal contaminants from dry products like grains, seed, or pet food.
- Grate Magnets: Like plate magnets, grate magnets are also designed for dry ingredient applications. These magnetic separators are made up of several magnetic bars through which the product passes. The magnetic bars collect and remove ferrous contaminants from the product. There are many grate magnet designs suited to various product types, such as flour, grain, sugar, and many more.
- Rotary Magnets: These magnets are most effective for dry, sticky, and difficult-to-flow products where bridging is an issue, such as dairy powders or sugar.
- Inline Magnets: These types of magnetic separators include designs suited to both dry and wet applications, and high-velocity product lines, pump lines and pneumatic transfers.
Want to learn more about how magnetic separators can keep your food products safe and pure? Be sure to check out our blog covering 5 key HACCP principles related to magnets, which are the cornerstone of any effective magnetic separation food safety management system.
What Are a Few Common Challenges in Food Processing Lines?
One of the main challenges in using magnetic separators in the food industry is the need to make sure that the food products are not contaminated by the magnet itself. To address this concern, many facilities use inline magnets for food processing, with stainless steel alloys that are much less prone to corrosion and are easy to clean and sanitize. However, certain products and processing lines can still present unique challenges when it comes to removing metal contaminants. For example:
- Sticky and Abrasive Products: Sticky and abrasive products, such as sugar and cereal, can wear down processing equipment and magnets. Magnattack® has developed a wear-resistance technology, Dura-Slik®, which protects the magnets from abrasive products and wear.
- High-velocity powder lines: The Magnattack® Spherical Pneumatic Transfer Magnet and Powder Transfer Magnet are great solutions for high-velocity pneumatic lines and great alternatives to conventional bullet-style and cartridge-style magnets. These highly effective Spherical magnet designs effectively collect and retain metal contamination, as well as minimize bulk density breakdown and blockage.
- Dairy products: It is essential that magnetic separators for dairy products have a sanitary design with no crevices or cracks where a build-up of product can occur. Magnattack® has a variety of dairy-grade, USDA-Accepted sanitary designs for a variety of applications.
Another challenge food processors encounter is removing fragments which can damage expensive machinery, from the product. In these cases, some solutions can include sieves and filters, which will collect the contamination and prevent damage from occurring.
Simply put, magnetic separators are an essential component of the food processing industry because they help remove ferromagnetic contaminants from food products, increasing the safety and purity of your food. That’s why partnering with an experienced magnetic separation provider is so important.
Magnattack®: Your Trusted Choice for Foreign Metal Control
Magnattack® understands the importance of keeping your food safe for consumers. We’ve provided food manufacturers with dependable solutions that bolster their approach to foreign metal control for over 50 years. Start a conversation with our expert team, or schedule a free consultation to learn more.