Your Guide to Understanding How Pet Food Is Made
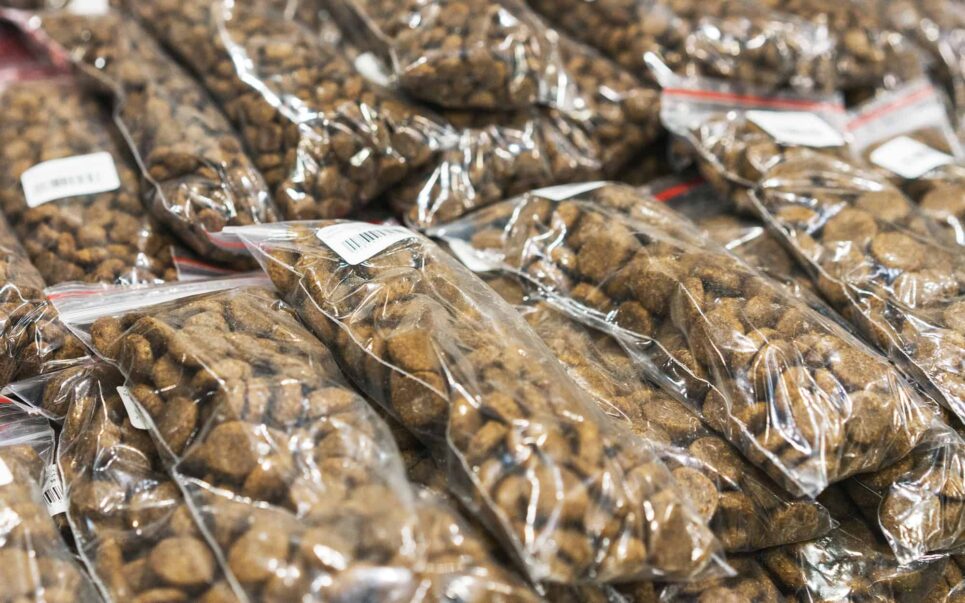
From selecting a reliable supplier to final packaging, every step in the pet food manufacturing process is carefully taken to ensure a quality, safe product.
Read on to learn more about how pet food is made.
Steps for Pet Food Manufacturing
Selecting Trusted Ingredient Suppliers
First and foremost, pet food is made by partnering with trustworthy suppliers. Suppliers are thoroughly examined for their quality control procedures and adherence to good manufacturing practices. This ensures that the ingredients they provide meet the highest standards. Once the suppliers are approved, each incoming ingredient is carefully inspected according to the company’s specifications. This extra step helps maintain the consistency and quality of the pet food.
Designing a Secure, Hygienic Facility
Pet food and treat manufacturing facilities are specially designed to ensure that pet food is safe and free from contamination. From the use of stainless steel equipment to protective coatings on floors and walls, every detail is carefully thought out to maintain hygiene throughout the manufacturing process. Handwashing stations and foot baths are installed to further prevent any unwanted bacteria from entering the production area, while positive airflow and established walking patterns minimize the risk of contamination. The perimeter, internal area, equipment, and ingredients are also closely monitored to ensure the highest level of safety.
Inspecting and Testing Ingredients
At pet food facilities, ingredients arrive in various ways, from bulk shipments in railcars and bags to refrigerated trucks for meat such as beef, poultry, and fish. But before these ingredients make it into the bowl, they undergo a thorough assessment and testing process.
Manufacturers inspect the integrity of container seals and the cleanliness of hoppers to ensure safe handling during transportation. They also make sure that tanker trucks are washed before loading and maintained at the correct temperature. The presence of metals in incoming ingredients can also be checked using magnetic separators to determine contamination levels and quality of ingredients.
Next, the ingredients are meticulously scrutinized for specific nutrient and grading specifications. From protein and fat content to moisture levels and antioxidant levels, every aspect is checked to ensure nutritional quality. Manufacturers also keep an eye out for any bacteria, spoilage, infestation, or toxins that could potentially harm pets.
Continuously Monitor During Manufacturing
Throughout the pet food cooking, shaping, and drying process, pet food is made using strict measures that guarantee the highest standards. From pH testing to removing and screening for metals, every step is carefully monitored. Dry and semi-moist food is cooked and shaped using an interesting extruder, similar to how cereal and pasta are made. The food is pushed through a die plate with specific shape and size holes, then cut to the desired size and transferred to a dryer. Natural flavors are added and, once cooled, the food is ready for packaging. Wet food, on the other hand, is poured into cans, vacuum-sealed, and sterilized in a heat and steam chamber. The main difference between dry and wet pet food is the moisture content, with wet food containing between 70-80%. Fresh pet food is made using fresh meat or poultry, not cooked at high temperatures, and does not use preservatives. It has a shorter shelf life and must be refrigerated.
Taking Safety Precautions During Packaging
Regular testing and inspection continues even after pet food is made and leaves the production line. Even during the packaging phase, multiple checks and tests are carried out to guarantee a safe product. These include verifying the correct mix and weight of the product, ensuring accurate barcodes and date codes for traceability, reviewing container and packaging integrity, and checking seal quality. Additional tests are conducted to ensure the food’s quality and safety, such as environmental bacteria testing, pH testing, moisture checks, and product consistency evaluations.
Considering Pet Food Manufacturing Regulations
The Federal Food, Drug and Cosmetic Act (FFDCA) has been in place since 1938. But in 2011, the Food Safety Modernization Act (FSMA) brought about even more comprehensive changes to pet food regulation, emphasizing the prevention of foodborne illnesses.
Under FSMA, pet food manufacturers must implement Current Good Manufacturing Practices (CGMPs), which are steps that help ensure food is produced in safe environments. This ensures that potential hazards, such as physical, chemical, and biological risks, are proactively addressed. Additionally, pet food makers must also comply with regulations set by the Federal Trade Commission (FTC) for labeling and advertising claims and the U.S. Department of Agriculture (USDA) for meat quality standards.
State registration is also required for pet food products before they can be sold within state borders. This process involves evaluations of products and labels to ensure compliance with state requirements. State regulators play a crucial role in product recalls, as they can quickly identify affected products and respond accordingly.
Pet food is highly regulated. Learn about pet food manufacturing regulations to prevent recalls and ensure your product is safe and nutritious for pets.
Remove and Screen for Metals in Your Pet Food Products With MagnattackⓇ
Metal contamination in pet food can be a serious health risk, which is why manufacturers are turning to magnetic separation technology from MagnattackⓇ. Our range of magnetic separators has been proven effective in reducing the risks of metal contamination in pet food:
- Our self-cleaning separator is ideal for incoming raw dry materials like grain, protein meals, and more.
- For dry ingredients, such as meals, powders, and grains, our easy-to-clean manual-clean drawer magnet is a must-have. Keep your ingredients pure and free from metal debris.
- Our inline magnet is perfect for wet products such as meat emulsions and slurries, ensuring a metal-free final product.
- And for powders, grains, premixes, and palatants, our pneumatic line magnet is the answer. Say goodbye to metal contaminants and hello to peace of mind.
- Worried about temperature or abrasive products? Our magnets are designed to handle it all. They’re sanitary, compliant, and easy to clean and maintain. Plus, our high-grade magnetics ensure longevity and consistent magnet strength.
Contact us today to learn more about our magnetic separators for pet food applications.