Reducing Metal From Your Meat Rendering Process
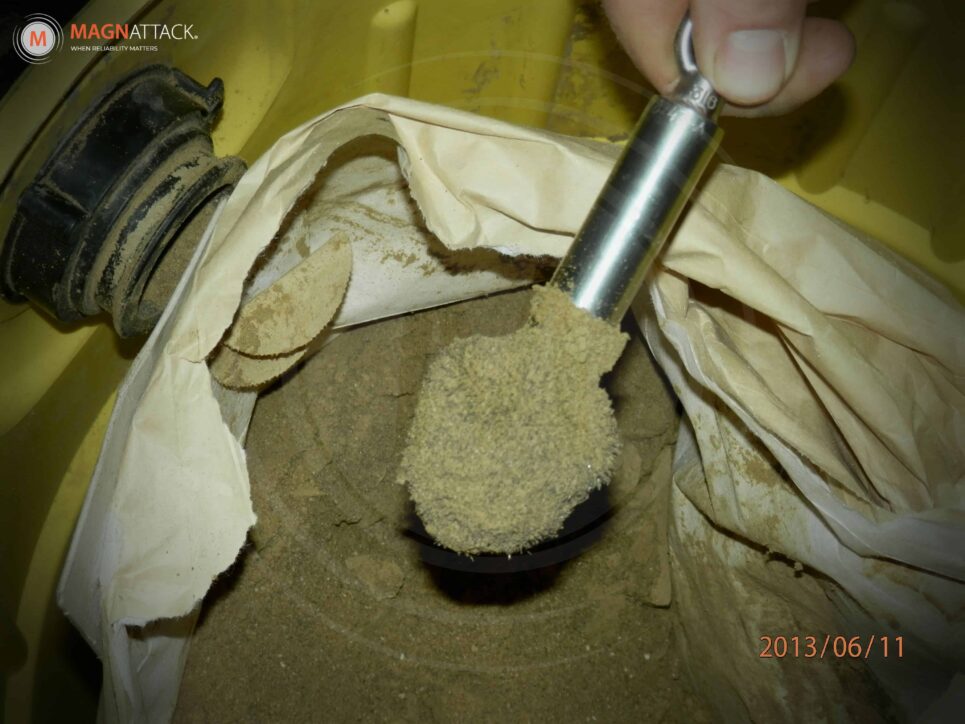
From tallow used in soap to protein meals found in pet food, meat rendering is a very significant industry. When it comes to ensuring food safety, the meat rendering process has an issue that is often much more severe than in other food processing industries – metal contamination. By improving metal fragment controls in the meat rendering process, and reducing the levels of metal contamination, renderers can provide their clients with better quality and more valuable products.
Metal contamination can wreak havoc on the quality and safety of your rendered products, which as a result, can negatively impact your exports to clients. But fear not! In this blog, we’ll uncover the common sources of metal contamination, explore how to enhance the safety of your meat rendering procedures and empower your facility with practical tips to better secure your operations.
What Is Meat Rendering?
Meat rendering is a critical process within the food processing industry that transforms animal by-products into useful ingredients. It converts raw materials—bones, fats, offal—into substances like tallow, protein meals, and bone, feather, and blood meal. The finished product finds applications in a wide variety of sectors, ranging from agriculture to cosmetics to pet food and more.
The meat rendering process encompasses several stages that work in harmony to extract each usable component from the animal or raw material. First, they are subjected to grinding processes, which break them down into smaller, more manageable pieces.
The next phase is cooking. Heat is applied to the ground materials, initiating the breakdown of fats and proteins. This thermal treatment aids in the separation of your desired components from the rest of the mixture.
Once the cooking is complete, the mixture undergoes separation. You can use several different techniques to isolate your desired substance from the remaining material, including centrifugation, filtration, or the use of decanters.
However, it’s important to note metal contamination occurs not only just during these stages but way before the process even begins! Let’s have a look at the various causes of metal fragments in meat rendering:
3 Main Sources of Metal Contamination in the Meat Rendering Process
When it comes to the meat rendering process, there are three main culprits of metal contamination:
- Equipment Wear and Tear: Over time, the machinery used in the meat rendering process wears down, creating loose metal particles, which then contaminate the rendered products. During the rendering process, machinery and equipment, such as the hammer mills, screens, blades, grinders, etc, can come into contact with each other or with other abrasive items that are in the process, causing wear and tear of this high-impact machinery.
- Maintenance and Repair: During maintenance activities, metal shavings, tools, fasteners, and other metal items can find their way into the process, which can lead to contamination and damage to machinery.
- Raw Material Contamination: Metal contaminants can enter the rendering process through the raw materials themselves. This is very common with ovine products, as the drenching capsule springs remain in the sheep and get ground up along with the meat meal. Poultry and feather meal processing also tend to have metal contamination present in the raw materials. This is due to the magnetic stone contamination in the gut.
What Procedures Can Help Reduce Metal Fragments from the Meat Rendering Process?
Looking to reduce the metal fragments from your meat rendering process and please your clients? With a few tips and tricks, it’s never been easier to detect and remove metal contaminants. Here are a few procedures you ought to consider.
Invest in Magnetic Separation Equipment
There’s a wide variety of magnetic food separators to choose from, and not all of them are created equal. On paper, you might have the right equipment, but investing in magnets that can withstand the abrasive nature of the meat rendering process can take your production to a whole new level.
So, let’s take a look at a few types of magnetic separation equipment poised to revolutionize the way you approach your meat rendering process:
- Mag-Ram® Self-Cleaning Magnet for Bulk Outloading: The Mag-Ram® Self-Cleaning Magnet is a highly efficient solution for continuous removal of metal contaminants. It combines the benefits of self-cleaning technology with powerful magnetic force, ensuring the removal of ferrous and weakly magnetic particles from the material flow. Its self-cleaning capabilities are designed to minimize or eliminate downtime altogether, and maximize productivity, which contributes to a safer rendering process, with no jamming or blocking issues! The Mag-Ram® cleaning cycle can be configured to clean before, after, or during production runs, with the Magnetic Rams being cleaned one at a time or simultaneously. This magnetic separator works exceptionally with the high levels of metal contamination typical to the meat rendering industry.
- Spherical Pneumatic Transfer Magnet: The Spherical Pneumatic Transfer Magnet is an innovative solution that performs exceptionally well in meat rendering. Because of its resilience in high-flow and abrasive applications, it effectively removes metal contaminants and prevents entry into subsequent processing stages. Even better, its simple design leads to easy installation and maintenance, which makes it a valuable addition to any meat rendering facility. These are a very effective alternative to conventional cartridge and bullet-style magnets.
- Dual Round Nose Plate Magnet: When it comes to challenging high-volume applications, the Dual Round Nose Plate Magnet emerges as an excellent solution. This magnet is specifically designed to handle difficult-to-flow materials, ensuring smooth and efficient processing. Its powerful magnetic force allows it to effortlessly capture chunky contaminants, such as nails and bolts. What truly sets this magnet apart, however, is its ability to achieve optimal metal separation without causing any significant disruption to the flow of the product. The magnetic plates are adjustable, and this magnetic separation unit is also suitable for Crax applications!
Conduct Magnet Testing
One of the most beneficial steps in improving metal fragment control in your meat rendering process is annual magnet testing. And yes, while you may already have mag separators in place to remove contaminants from your product, it’s entirely possible they’ve lost their strength or there is another issue that may be reducing their effectiveness. Luckily, by conducting routine testing of your magnets’ effectiveness, any issues or deterioration can be easily identified and addressed, which helps you reduce the risk of metal contamination in your final product. By having a pure final product, you can avoid issues such as quarantined shipments, unhappy clients, downgraded products causing reduced value, as well as brand name damage and loss of confidence.
Cultivate a Safer Meat Rendering Process With Magnattack®
When it comes to creating a safer meat rendering process, there’s a name that stands out among the rest: Magnattack®. With over five decades of experience, we know what it takes to effectively reduce metal contamination risks and elevate food safety standards.
Trusted by processors worldwide, our innovative solutions are designed to address the unique challenges of the meat rendering industry. From dry applications to wet applications, our magnetic separation equipment is meticulously manufactured to deliver outstanding results.
Start a conversation today, and learn why rendering facilities choose Magnattack® to help them create a safer meat rendering process.