How to Reduce Physical Contamination in Food Processing
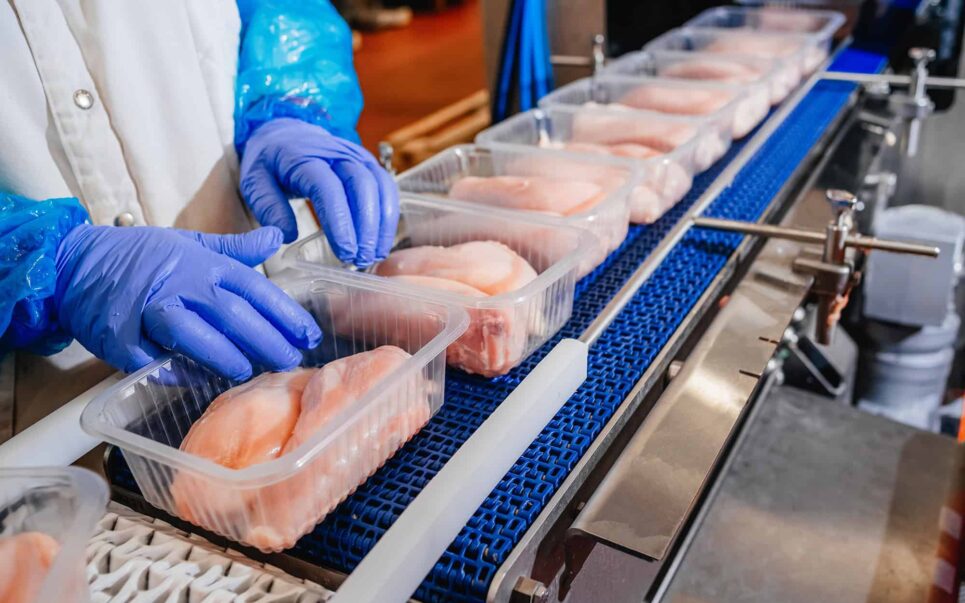
When it comes to uninvited guests at the dinner table, metal contamination is one of the most nefarious. It’s also an easily-avoidable problem. In this blog, we’ll dive into a few effective strategies for reducing physical contamination in food products.
Three Effective Strategies for Reducing Physical Contamination in Food Products
Coordinating legislative pressures, food processing facilities across the globe can adopt these three strategies to reduce metal contamination in their goods.
1. Iron Out Liabilities by Creating a Safety-First Culture
Food safety management systems are essential to reduce physical contamination in food. First, they are an easy way to identify any potential hazards in your food production process. Second, if any hazards are found, the systems outline corrective actions, response plans, and best-practices.
When creating safety first-culture, adhere to Hazard Analysis & Critical Control Points (HACCP) standards, which are a vital aspect in maintaining compliance.
2. Reduce Metal Contamination With Magnetic Separation Equipment & Metal Detectors
Installing both metal detectors and magnetic separators is essential for effectively reducing physical contamination in your food products. They both complement one another in order to achieve what the other cannot. For example, metal detectors typically target larger contaminants, but can miss those small, dust-like metal fragments that magnets can easily collect. Some of these can present in food products as black spots, causing consumer concerns and complaints. Let’s have a look at the various types of magnetic separators for both dry and wet food processing lines.
Dry Application Magnetic Separators
- Mag-Ram® Automatic Self-Cleaning Magnet: The Mag-Ram® requires little to no operator intervention. The cleaning can be set for during, before, or after production runs, with no need to stop the process. Each magnet is the ram of a pneumatic cylinder, which means there is no ‘walking’ or ‘jamming’ when attempting to clean multiple bars simultaneously. The Mag-Ram® is also extremely hygienic, due to the absence of stainless-steel sleeves which tend to build up with unclean product and can become a recontamination issue. It’s important to note that sleeve-type magnets are specifically excluded in the current HACCP magnet standard.
- Rapidclean® Drawer Magnets: The Rapidclean® Drawer Magnet is a dust-tight, sanitary design grate magnet, engineered to capture and retain even the smallest foreign metal fragments, including work-hardened stainless steel. With a cleaning operation that is performed entirely outside of the product stream, operators can access, inspect, and clean this magnet quickly and easily without the risks of recontamination during cleaning.
- Rapidclean® Rotary Magnet: This magnetic separator is designed for powder product streams that tend to plug or bridge. The rotary action prevents this from occurring as it breaks apart soft lumps and sticky material.
- Bullnose Plate Magnet: The Bullnose Plate Magnet takes the conventional “hump-magnet” to a whole new level of separation efficiency. The Bullnose Plate Magnet Unit can be supplied with a single or dual plate, depending on whether the application is a straight gravity drop or a sloping chute. The Bullnose Plate Magnets are mounted inside hinged doors for easy accessibility, inspection, and cleaning. These units are fully adjustable, which enables you to set the magnets in the most ideal position to maximize separation efficiency, without blocking product flow.
- Spherical Pneumatic Line Magnet: This pneumatic convey line magnet effectively captures and retains even the smallest metal fines, chips, fine wear iron, and even rust flakes in high-velocity flow applications. The bellied housing around the aerodynamic magnet minimizes pressure change and prevents particle breakdown or bulk density change to the product. The Spherical design has significant advantages over more conventional shuttle, canister and bullet-type magnet designs, particularly related to retention of weakly magnetic fragments against the flow of product.
- Powder Transfer Magnet: The Powder Transfer Magnet is a high-intensity, sanitary design magnetic separator, engineered specifically for sensitive powder applications such as in dairy, nutraceutical, and pharmaceutical plants. This separator features high-intensity Acutex™ Probe Magnets configured to remove even the smallest and weakly-magnetic fragments (including work-hardened stainless steel fragments) in high-velocity pneumatic convey lines.
- RE80® Separation Shafts: RE80® Separation Shafts are designed to split the flow of the product and maximize product-to-magnet contact. These magnets effectively extract splinters of stainless steel, magnetic stone fragments, and >98% of tramp iron and ferrous fines from dry products.
Wet Application Magnetic Separators
- Pressure Pipeline Separator: The Magnattack® Liquid Pressure Pipeline Separator is engineered to efficiently extract magnetic fragments (including work-hardened stainless steel) from liquid food lines such as soups, chocolate, sauces, etc. The system features a single or double set of powerful RE80®HT +11,000 Gauss magnet elements which intercept the flow of product and securely retain foreign metal contaminants.
- Emulsion and Slurry Pipeline Separator: Installed in high-viscosity product lines, this magnetic separator removes metal particles from thick emulsion or slurry products like peanut butter, cheese, meat emulsions and meat slurries, pastes, purees, ice cream, etc. These magnets are also available in a very effective quick-clean configuration, reducing operator time during cleaning.
With a complete suite of equipment for a wide variety of industries, Magnattack® is your one-stop-shop for heavy-duty magnetic separators.
3. Invest in Magnet Validations and Risk Assessments
Unfortunately, magnetic separators degrade over time, which means that there has to be a way to properly and effectively monitor the effectiveness of your magnetic separation equipment.
That’s exactly why magnet validations and risk assessments are so crucial. This service includes a 3rd party, HACCP-Certified Magnet Validation Report, which will supply you with detailed information on the efficiency of your foreign metal fragment controls, including:
- Status of each magnet, including strength, condition, coverage, retention, and more.
- Identifying potential hazards and safety risks and tips on how to reduce them
- Requirement for new magnetic separation systems (if applicable)
Implementing annual magnet validations into food safety management systems helps food production plants:
- Boost quality control and increase food safety
- Comply with current industry standards
- Protect brand reputation
- Reduce risks of product recalls
- Comply with customer’s requirements and satisfy auditors
Magnattack®: Reducing Physical Contamination in Food Since 1969
Need to reduce physical contamination in your food products? Look no further than Magnattack®. As a leading provider of magnetic separation equipment for wet and dry applications, we deliver robust solutions to keep your food safe. Start a conversation to learn more. We’re just a click away.