50 Years In Food Industry Magnetics
This year Magnattack® Global celebrates a milestone 50 years in food industry magnetics!
From humble beginnings as a one-man-operation servicing the local Sydney and surrounding areas, the company has expanded to a global team wholly focused on solving foreign metal fragment control problems for the food industry worldwide – many of whom have followed Magnattack® Global through this journey.
“I would say that the Magnattack teams success, not only here in Australia but evidently in the US as well, is a testimony to their focus on developing systems that are tailored to the food industrys needs. It’s great to see that the company is still in the family as well – I used to work with Bill, now we’re regularly in contact with Rob and Kevin.”
Quality Engineer – an Australian rice mill.
In 1969 the company started out as W. J. Baker and Co and operated out of a small garage in Thirroul NSW Australia. The founder recognized a need in the food and grain industry for effective magnetic separators. Working closely with quality assurance technicians and plant operators, it became his mission to develop new and advanced magnetic separators that would overcome problems experienced with magnets available at the time. These problems included cleaning difficulties, product stream blockages, and hygiene issues.
Shortly after this, an office and manufacturing facility was purchased in Bulli NSW to keep up with the rising demand.
_
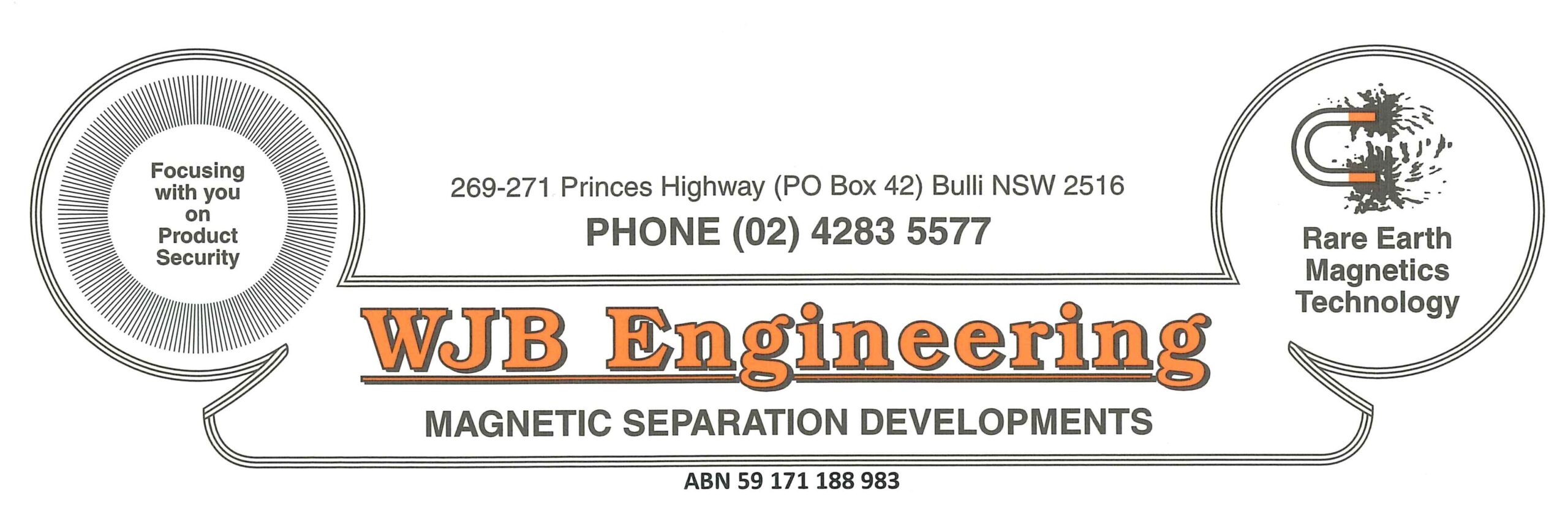
_
The company began supplying bars and grate-style magnets for dry applications such as milling, and probes and liquid-line units for various liquids including soup. It has since progressed to the entire food industry, including dairy, pet food, snacks and confectionery, meat and poultry processing, and bakeries.
“Our mission has always been to solve the issues the food industry has experienced with metal contamination – not only the problem itself but also the ongoing problems the industry experiences with designs that are difficult to clean, handle, and don’t comply with the standards of the current day. We’ve studied their problems, listened to the customer, and built our designs around the needs we’ve learnt about over all these years.”
Kevin Baker – Director, Magnattack Global.
We keep in close contact with our customers, including many who have partnered with us for several decades.
“I’ve been working with Magnattack for the past 26 years and I’ve always found them keen to help. They have the ability to improve our designs, and they listen to you. You get what you ask for and they will tell you the truth about whether you have it right or wrong. You cant walk past that level of commitment!”
Quality Manager – a gluten manufacturing company, Australia.
1990’s
In the early 1990’s the company developed RE80® Magnetics Technology. This technology is the guarantee to our clients that Magnattack® magnetic separators do not contain inferior low-cost magnets, and is the assurance of proven long-term magnet strength life and resistance to oxygen absorption and resonant vibration.
In 1996 we developed the Quick-Clean Drawer Magnets. These designs were an answer to ongoing complaints from the Japanese customers of the starch and rice industries in Australia.
_




_
In 1997 following a clients trouble with Finger Pot Magnets in their liquid lines, WJB invented the Liquid Pressure Pipeline Magnet. Commonly referred to as the ‘PPS’, the system was engineered to overcome blockages, leaks, and cleaning difficulties. 20 years on, the PPS is still the most effective magnet design for metal fragment control in liquid lines.
_




_
In 1995 we supplied a bakery client with the first-ever Spherical Pneumatic Transfer Magnet. The Spherical Magnet is one of our most unique systems and provides highly effective and aerodynamic separation of metals in flour and other powdered product lines. Following the immediate success of the first install, the magnet became popular in flour mills across Australia. Several units have been in operation for 15+ years.
_




_
2000’s
In 2001 WJB Engineering became the first company to be endorsed by HACCP International as a provider of magnetic separation technologies. This endorsement signified our long-standing committal to sanitary metal fragment control systems for the food industry.
_
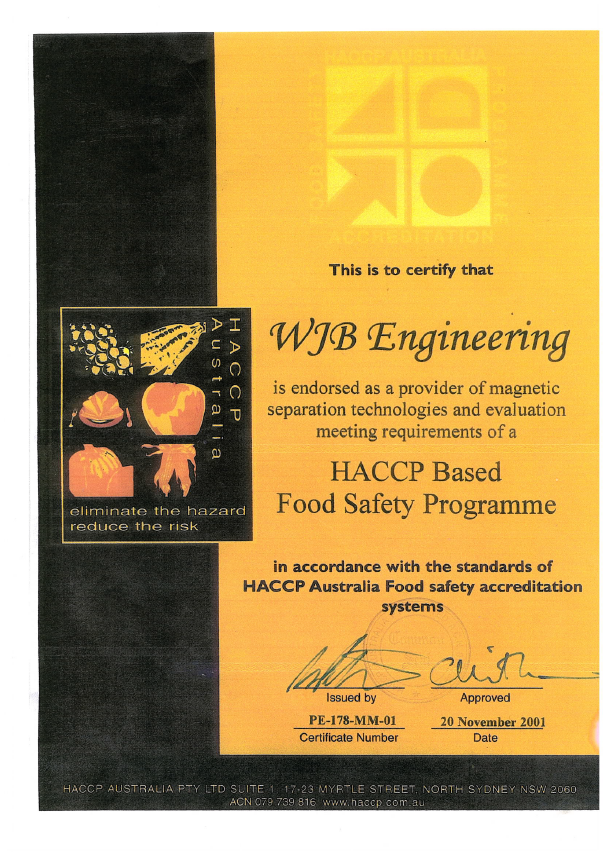
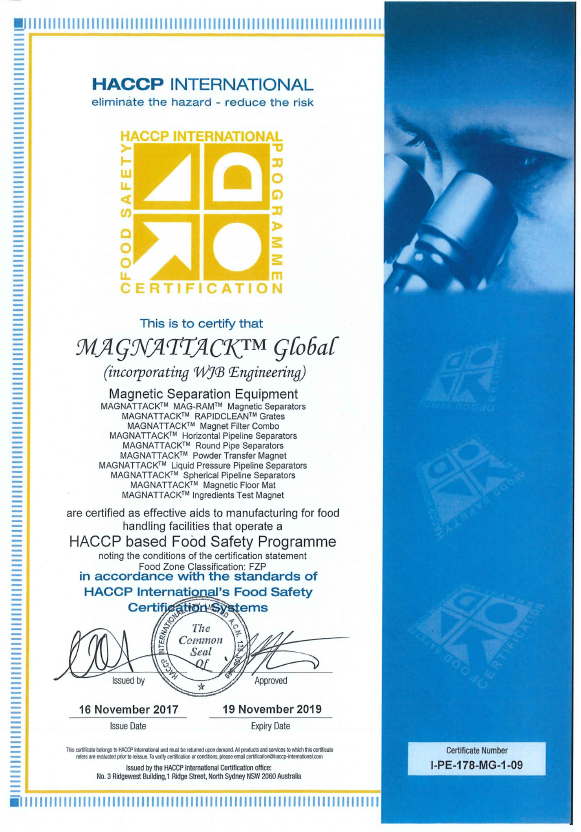
_
Throughout 2006 we designed and released the new Rapidclean® Grate Magnet. In a time where stainless-steel sleeves, cleaning difficulties, and safety issues were common of existing grate magnet technology, the Rapidclean® stood out with its self-supporting design, sanitary dust-tight housing, and a cleaning operation performed wholly outside of the product stream – reducing recontamination risks. These features are still considered highly important by hundreds of Rapidclean® customers today.
_



_
In 2007 and 2008, WJB Engineering formed a partnership with AMR Consulting. AMR Consulting provides HACCP-endorsed Magnet Validation Reports that help food industry clients understand the status of their magnetics, identify areas of risk, and implement measures/changes to reduce these risks. Prior to this, WJB Engineering had been helping clients with basic magnet audits since before 1999.
“It’s rewarding to reflect over the past half-century & see the progress we’ve made in food safety & metal fragment control. One of the most exciting years was 2008, the introduction of the Mag-Ram. It’s been a game-changer, an industry-leader in self-cleaning magnet technology, and we’re proud to be able to offer such an effective magnet to our clients.”
Rob Baker – Director, Magnattack Global
After extensive research and development, the first Mag-Ram® Self-Cleaning Separator was built, delivered, and installed at a grain facility in Adelaide, South Australia. The install was successful and marked the beginning of an era in effective self-cleaning magnets. Over 11 years the Mag-Ram® has continuously evolved to suit current-day food industry applications, making it the most versatile, successful, and efficient automatic cleaning separator on the market today.
_




_
2010’s
In 2010, we had the largest single order of Mag-Ram® Self-Cleaning Separators to date. Multiple Mag-Ram® units were manufactured and personally delivered to a client in Sydney NSW. All of these units are still in operation today.
Following substantial growth in the company, we moved in 2011 to a larger premises in Unanderra NSW. The increased office and manufacturing facilities enabled us to provide faster deliveries and increased our capacity to develop advanced solutions in answer to the growing needs and increased regulations in the food industry.
Also in 2011 was the re-brand of WJB Engineering to Magnattack® Global. For several years, ‘ Magnattack’ had been the brand-name of the magnetic separators manufactured by the company. Following the expansion of the company into the United States, the company began trading as Magnattack® Global. A press release at the time stated that “our movement into the global market allows us to further help food processing companies to increase product safety and their control of metal fragment contamination in compliance with HACCP, BRC, FSMA, and other relevant regulatory structures”.
_
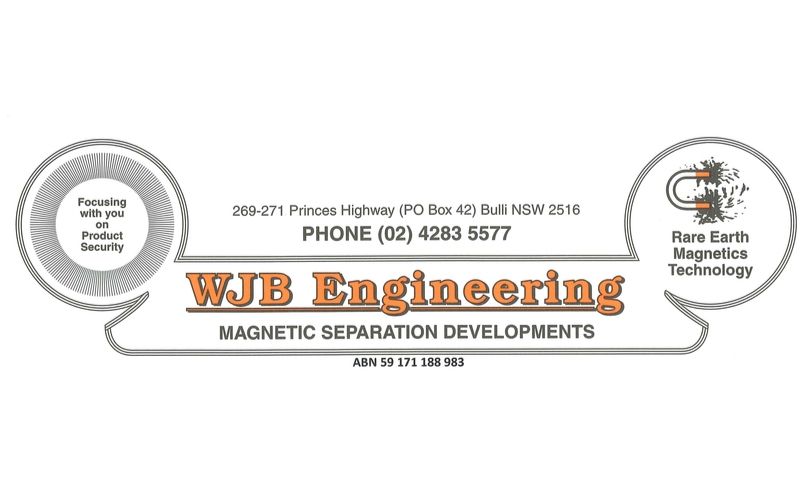
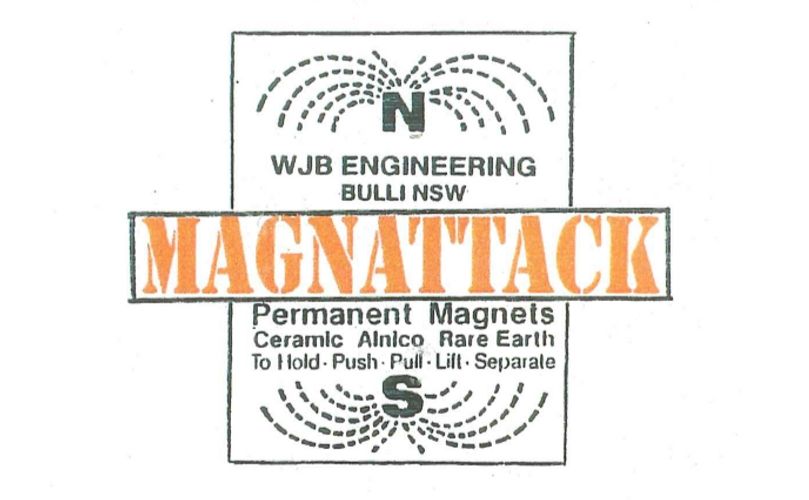
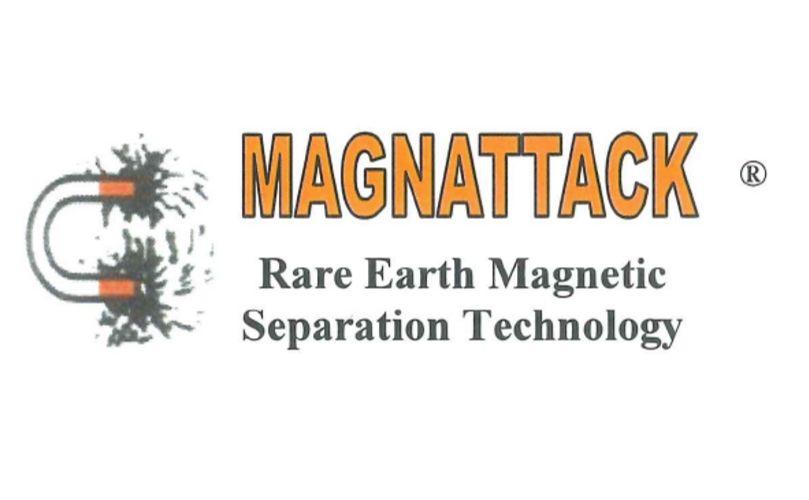

_
FSMA (Food Safety Modernization Act) was relatively new at the time, having just been signed into law by then-President Barack Obama on Jan 4, 2011. To this day, we are still helping US clients meet FSMA requirements with AMR Magnet Validation Reports & Magnattack magnetic separators.
In 2013 we established our first sales team in the United States.
“It’s an exciting time at Magnattack Global right now, especially in the United States. We’ve had presense here for several years and it’s clear to see the industry’s need for the Magnattack RE80 systems. The customers we have now are greatly appreciative and amazed at the effectiveness of the unique systems we have, and the success they’ve had is something we will continue to replicate with several more in the coming years.”
Russell Paskewitz – Technical Sales & Support Manager, USA
2012 marked the development of the Mag-Stride™ Magnetic Mat, which was designed to reduce food safety risks by restricting ferrous metal being walked into sensitive production areas. The Magnetic Mat was eagerly accepted by many food industry clients as a positive contribution to food safety.
_


_
2013 was the year in which Magnattack® became specifically aware of the challenges that the rendering industry was facing. This was after a NSW-based renderer approached us to help solve a very difficult metal contamination issue that is particularly associated with ovine meal. We needed to consider an effective magnet able to adequately screen the product without hindering product flow. In customizing a solution to overcome the challenges of moisture level, fats, humidity, dust, and abrasion in meal, it became evident how suitable the Mag-Ram® was for enhancing the product purity of all types of protein meals and meat rendering applications.
The Acutex™ Probe Magnet was first designed and manufactured by Magnattack® Global in 2014. The probe has a distinctive lachrymiform shape with a large highly magnetic surface area on the underside, tapering to a point on the upper. Along with improved product flow and reduced recontamination risks, the Acutex™ Probe offers a great many beneficial enhancements to metal fragment control in both liquid and dry product lines.
_


_
Several magnetic separator designs, including the Mag-Ram®, Rapidclean®, Round Pipe Separator, and Powder Transfer Magnet received USDA Dairy Acceptance in 2015. This acceptance offers peace of mind to dairy and critical hygiene customers that Magnattack® has taken extensive measures to ensure magnetic separation developments are of the highest sanitary design and materials.
In 2017 the Mag-Ram® Self Cleaning Separator won the US Dairy Innovations Showcase at Process Expo – a testimony to its sanitary design, unique function, and revolutionary advantages to the industry. The Mag-Ram® was recognized as having a clear distinction in the marketplace and a breakthrough in the magnetic separation world.
_
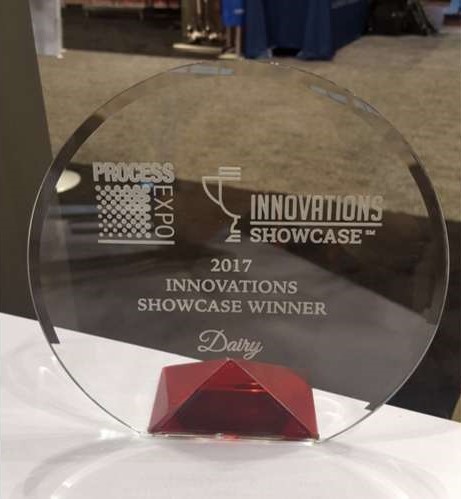
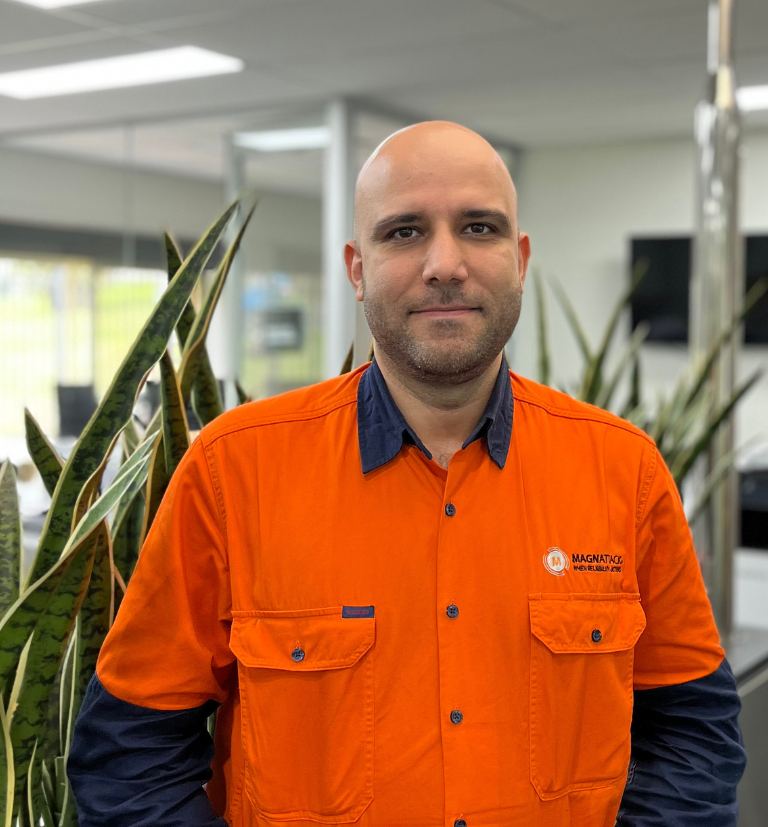
_
2018 was a milestone year for Magnattack®. During that year we released both Dura-Slik® Abrasion Reduction Technology and the Emulsion & Slurry Pipeline Separator to the market, and also celebrated the 10th year anniversary of the Mag-Ram®.
Following extensive trials and comparisons in abrasive product applications such as grain, rice, meat rendering, and pet food, it was proven that Dura-Slik® imparted increased abrasion resistance and anti-stick properties to the surface of magnet probes and bars. This was a breakthrough in extending the longevity and durability of magnetic separators. Clients using Dura-Slik® Technology have reported positive deductions in pitting and abrasive wear to the surface of their magnets.
First developed and trialed in 2016 in answer to the needs of a multi-national pet food manufacturer, the Emulsion & Slurry Pipeline Magnet was found to be highly successful in the separation of ferrous metal and work-hardened stainless-steel fragments from thick, viscous slurries and liquids. The Emulsion Magnet went on to receive USDA Acceptance in both dairy and meat/poultry categories in January this year.
_
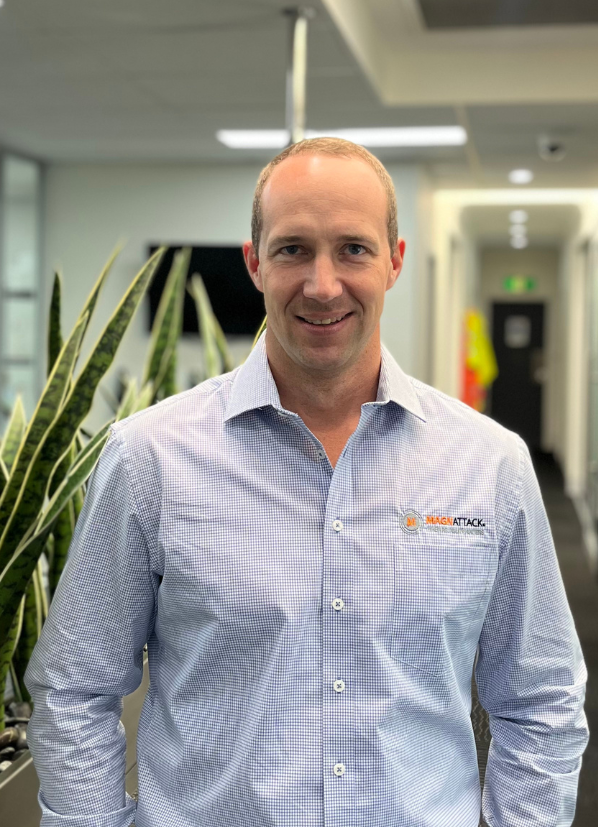
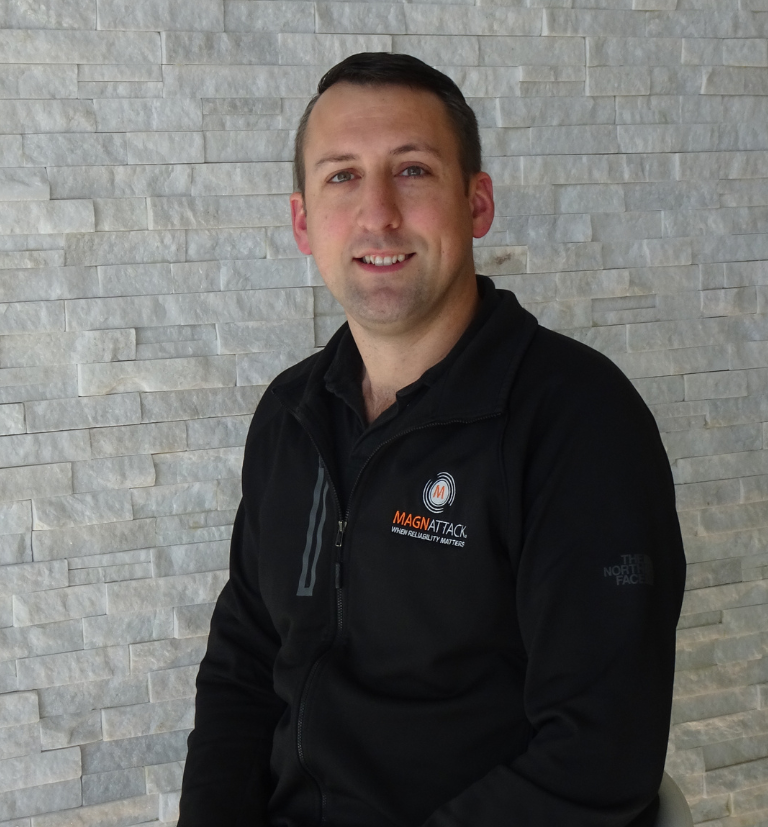
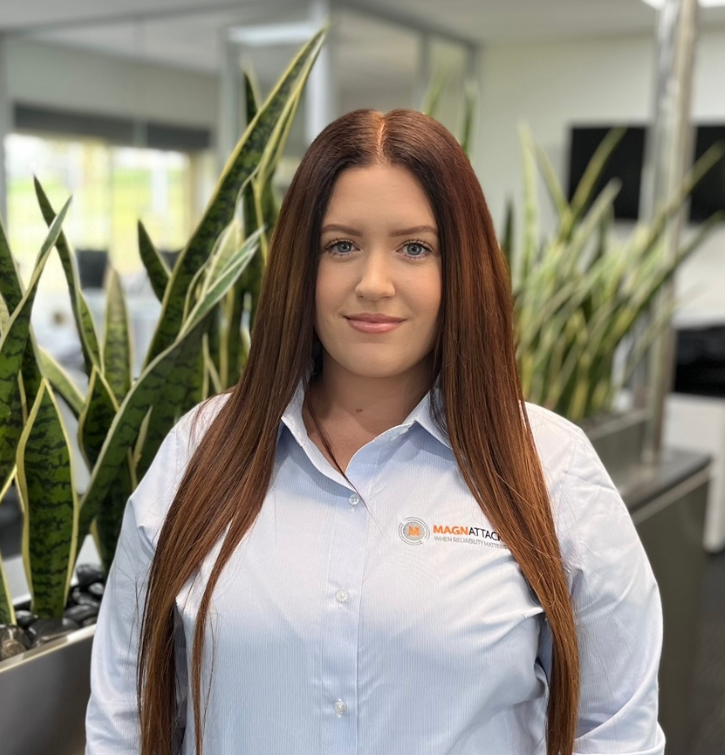
_
The Next 50 Years
To this day Magnattack® Global remains a family-owned and operated company.
For 50 years we have worked closely with the food industry to develop unique, effective, sanitary magnetic separator systems. We have been dedicated to being a reliable source for metal fragment control solutions to reduce contamination risks and improve food safety. For the next 50 years, we will continue to do the same.
We believe in continual innovation, listening to our customers, and the development of quality magnetic separation systems to solve metal fragment control problems experienced in the food industry today.
Our team of food industry magnetic separation experts are always available to help. Contact us here.